Currently, efficiency and productivity are fundamental to business success. Lean Manufacturing, a methodology focused on waste elimination and continuous improvement, has proven to be a powerful tool for achieving these objectives.
Since its origins at Toyota in the 1950s, Lean Manufacturing has been widely adopted in the automotive industry and has expanded its application to sectors such as manufacturing, healthcare, financial services, among others. This methodology has been demonstrated to be an effective way to increase quality, reduce costs, and improve customer satisfaction.
We will explore the history and foundations of Lean Manufacturing, as well as the most powerful tools that Lean engineers can use to achieve sustainable improvements in their operations. We will also address current and future challenges of implementing Lean Manufacturing, including how it can help companies adapt to the era of digitalization and sustainability.
If you are looking for effective tools to improve the efficiency and productivity of your company, keep reading.
The Origin of Toyota’s Success: The Story of Lean Manufacturing
Lean Manufacturing originated in Toyota’s factory in the 1950s as a response to the post-war challenges in Japan. During this time, the company faced issues with quality, costs, and efficiency due to a lack of resources and the need to produce affordable cars for the Japanese population. Taiichi Ohno, an engineer at Toyota, set out to solve these problems and developed a system focused on waste elimination and continuous improvement.
Ohno was inspired by the production system of American supermarkets to design the Kanban method, which allowed for just-in-time inventory control and eliminated excess production. Additionally, Ohno identified seven types of waste that occurred in the production process: overproduction, waiting time, transportation, processing, inventory, motion, and defects. With this in mind, Ohno developed the Just-In-Time (JIT) system, which focused on reducing waiting time and eliminating unnecessary inventories.
The application of Lean Manufacturing at Toyota was a resounding success, which led the company to become one of the most successful car manufacturers in the world. From there, Lean Manufacturing spread throughout the world and adapted to a wide range of industries and applications. Today, Lean Manufacturing is a widely used methodology in the industry and is considered a powerful tool for achieving sustainable improvements in efficiency and productivity.
What is Lean Manufacturing and what are its principles?
The term “lean manufacturing” was coined in the book “The Machine that Changed the World” by James Womack, Daniel Jones, and Daniel Roos in 1990. They used the term to describe Toyota’s production and how the company was revolutionizing car manufacturing compared to its Western competitors. The word “lean” refers to the elimination of any waste, excess, or unnecessary activity in production, resulting in a more efficient and competitive company.
Lean Manufacturing is based on five fundamental principles:
- Identify value: this involves understanding what the customer values and focusing on providing that value effectively.
- Value stream mapping: involves mapping the entire production process, from customer order to product delivery, identifying areas of waste and opportunities for improvement.
- Creating flow: once improvement opportunities are identified, a continuous flow of work should be created, eliminating bottlenecks and delays.
- Establishing just-in-time production: this means producing only what is needed, in the quantity needed, and at the time it is needed, reducing inventories and associated costs.
- Pursuing excellence: this principle involves a constant pursuit of improvement and waste elimination, to maintain efficiency and quality over time.
Lean Manufacturing has expanded into different areas, such as Lean Management and Lean Thinking, focused on efficient resource management and continuous improvement. These tools have allowed companies to be more competitive and adapt to constant market changes.
9 Key Techniques of Lean Manufacturing
Lean Manufacturing relies on various tools and techniques that aim to improve efficiency and quality in production. Here are some of them:
- Kaizen: A philosophy of continuous improvement that involves the participation of all workers in identifying and solving problems. It focuses on small daily improvements to achieve significant long-term results.
- 5S: A methodology for organizing and maintaining a clean and tidy workplace. The 5S are: Seiri (sorting), Seiton (straightening), Seiso (cleaning), Seiketsu (standardizing), and Shitsuke (sustaining).
- Poka Yoke: The implementation of devices or mechanisms to prevent errors or failures in production.
- Kanban: A production control system that relies on visual signals to indicate when a product should be produced or moved.
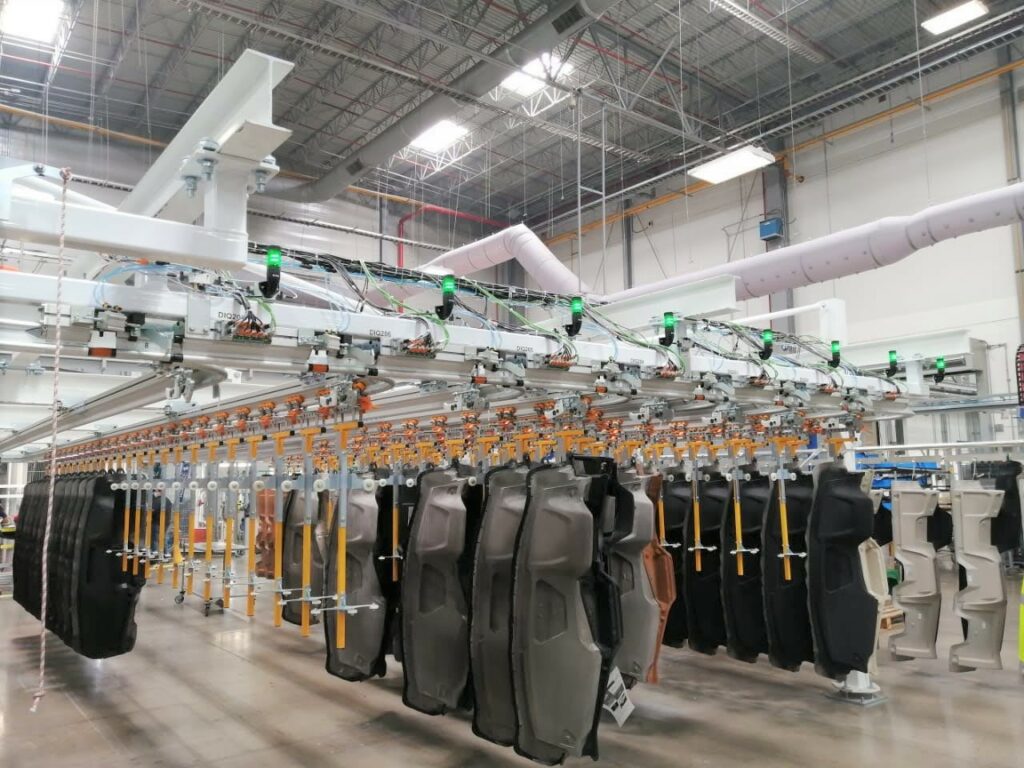
- Just in Time (JIT): The practice of producing only what is needed, in the quantity that is needed, and at the time it is needed, reducing inventories and associated costs.
- Andon: A visual signaling system that indicates problems or interruptions in production.
- Value Stream Mapping (VSM): A tool for mapping the entire production process, identifying areas of waste and opportunities for improvement.
- Jidoka: Refers to automation with a human touch. It involves stopping production in case of a problem, correcting it, and preventing it from recurring in the future.
- FIFO (First In, First Out): An inventory control technique that involves consuming the oldest materials or products first, to avoid obsolescence or waste of materials.
Each tool and technique is used to address different areas of production and continuously improve the process.
The future challenges of Lean Manufacturing: How to maintain relevance in a changing world?
Despite the numerous successes achieved by Lean Manufacturing, the continued adoption of disruptive technologies and changes in the way consumers buy and employees work present new challenges. The future of Lean Manufacturing will focus on three main areas: adaptability, digitalization, and sustainability.
Adaptability will be key to the success of Lean Manufacturing, as companies will need to quickly adjust to changes in market demand and technological disruption. Flexibility and agility will be fundamental to staying competitive.
Digitalization will also be essential to the future of Lean Manufacturing. Digital tools and technologies, such as the Internet of Things, data analytics, and artificial intelligence, can help improve efficiency and reduce production costs, as well as improve decision-making.
Lastly, sustainability will be a significant challenge for Lean Manufacturing. Companies must work to reduce their environmental impact and increase energy efficiency in production, as well as find ways to reduce the amount of waste generated.
To overcome these challenges, companies must continue to adopt a mindset of continuous improvement and be willing to adapt and evolve in a constantly changing business environment.
Optimization of internal logistics: key to the success of Lean Manufacturing
Internal logistics plays a fundamental role in the success of Lean Manufacturing. Its main objective is to ensure the delivery of necessary materials and components for the production process at the right time and in the right quantity, thus avoiding inventory accumulation or bottlenecks.
To achieve this, it is necessary to apply Lean Manufacturing techniques and tools such as value stream mapping, just-in-time production, and continuous improvement. Additionally, factors such as storage space design, route planning, and choosing reliable suppliers must be considered.
Some of the practices that can be implemented to improve internal logistics within the framework of Lean Manufacturing are:
- Implementing the kanban system: an inventory management method that uses visual signals to indicate when materials need to be replenished, such as the pick-to-light system.
- Applying the principle of the 5S: a methodology for organizing the workspace and increasing efficiency, based on five pillars: sorting, orderliness, cleanliness, standardization, and discipline.
- Using technology for supply chain tracking: tools such as radio frequency identification (RFID) systems for real-time tracking.
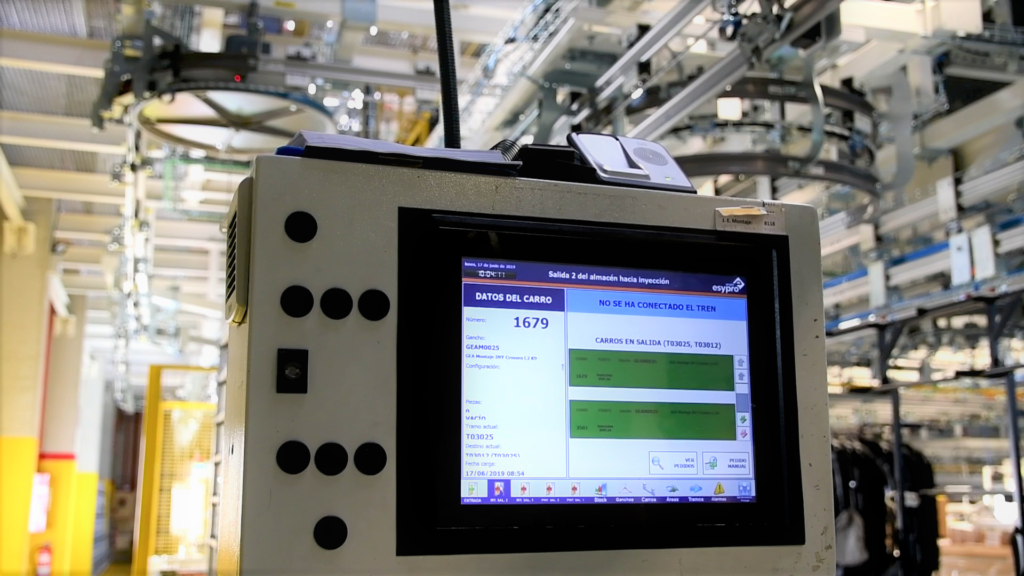
In summary, internal logistics is a key piece in the successful implementation of Lean Manufacturing. By improving efficiency in the delivery of materials and components, there is a significant reduction in production costs and an improvement in the quality of the final product. To achieve efficient internal logistics, it is recommended to work with experts in the field, such as Esypro, who can provide customized and effective solutions.
Contact us and discover how we can help you improve your internal logistics and take your company to the next level in Lean Manufacturing.