En la actualidad, la eficiencia y la productividad son fundamentales para el éxito empresarial. El Lean Manufacturing, una metodología enfocada en la eliminación de desperdicios y la mejora continua ha demostrado ser una herramienta poderosa para lograr estos objetivos.
Desde sus orígenes en Toyota en la década de 1950, el Lean Manufacturing ha sido ampliamente adoptado en la industria automotriz y ha expandido su aplicación en sectores como el de la manufactura, la salud, los servicios financieros, entre otros. Esta metodología ha demostrado ser una forma efectiva de aumentar la calidad, reducir los costos y mejorar la satisfacción del cliente.
Exploraremos la historia y los fundamentos del Lean Manufacturing, así como las herramientas más poderosas que los ingenieros Lean pueden utilizar para lograr mejoras sostenibles en sus operaciones. También abordaremos los retos actuales y futuros de la implementación del Lean Manufacturing, incluyendo cómo puede ayudar a las empresas a adaptarse a la era de la digitalización y la sostenibilidad. Si buscas herramientas efectivas para mejorar la eficiencia y productividad de tu empresa, sigue leyendo.
El origen del éxito de Toyota: La historia del Lean Manufacturing
El Lean Manufacturing se originó en la fábrica de Toyota en la década de 1950 como una respuesta a los desafíos de la posguerra en Japón. Durante este tiempo, la empresa se enfrentaba a problemas de calidad, costos y eficiencia debido a la falta de recursos y la necesidad de producir automóviles asequibles para la población japonesa. Taiichi Ohno, ingeniero de Toyota, se propuso solucionar estos problemas y desarrolló un sistema enfocado en la eliminación de desperdicios y la mejora continua.
Ohno se inspiró en el sistema de producción de supermercados estadounidenses para diseñar el método Kanban, que permitía un control justo a tiempo del inventario y eliminaba el exceso de producción. Además, Ohno identificó siete tipos de desperdicios que se producían en el proceso de producción: sobreproducción, tiempo de espera, transporte, procesamiento, inventario, movimiento y defectos. Con esto en mente, Ohno desarrolló el sistema Just In Time (JIT), que se centraba en la reducción del tiempo de espera y la eliminación de inventarios innecesarios.
La aplicación del Lean Manufacturing en Toyota fue un éxito rotundo, lo que llevó a la empresa a convertirse en uno de los fabricantes de automóviles más exitosos del mundo. A partir de allí, el Lean Manufacturing se extendió por todo el mundo y se adaptó a una amplia gama de industrias y aplicaciones. Hoy en día, el Lean Manufacturing es una metodología ampliamente utilizada en la industria y es considerada como una herramienta poderosa para lograr mejoras sostenibles en la eficiencia y la productividad.
¿Qué es el Lean Manufacturing y cuáles son sus principios?
El término «lean manufacturing» fue acuñado en el libro «The Machine that Changed the World» de James Womack, Daniel Jones y Daniel Roos en 1990. Ellos utilizaron el término para describir la producción de Toyota y cómo esta empresa estaba llevando a cabo una revolución en la fabricación de automóviles en comparación con sus competidores occidentales. La palabra «lean» se refiere a la eliminación de cualquier desperdicio, exceso o actividad innecesaria en la producción, lo que se traduce en una empresa más eficiente y competitiva.
El Lean Manufacturing se basa en cinco principios fundamentales:
- Identificar el valor: se trata de comprender lo que el cliente valora y enfocarse en proporcionar ese valor de manera efectiva.
- Mapeo del flujo de valor: implica mapear todo el proceso de producción, desde el pedido del cliente hasta la entrega del producto, identificando áreas de desperdicio y oportunidades de mejora.
- Creación de flujo: una vez identificadas las oportunidades de mejora, se debe crear un flujo continuo de trabajo, eliminando cuellos de botella y retrasos.
- Establecimiento de la producción justo a tiempo: significa producir solo lo que se necesita, en la cantidad que se necesita y en el momento en que se necesita, reduciendo los inventarios y los costos asociados.
- Perseguir la excelencia: este principio implica una búsqueda constante de mejora y eliminación de desperdicio, para mantener la eficiencia y la calidad en el tiempo.
El Lean Manufacturing se ha expandido en diferentes áreas, como el Lean Management y el Lean Thinking, enfocados en la gestión eficiente de recursos y la mejora continua. Estas herramientas han permitido a las empresas ser más competitivas y adaptarse a los constantes cambios del mercado.
9 técnicas clave del Lean Manufacturing
El Lean Manufacturing cuenta con diversas herramientas y técnicas que buscan mejorar la eficiencia y la calidad en la producción. A continuación, se presentan algunas de ellas:
- Kaizen: Es una filosofía de mejora continua que implica la participación de todos los trabajadores en la identificación y solución de problemas. Se enfoca en pequeñas mejoras diarias para lograr grandes resultados a largo plazo.
- 5S: Se trata de una metodología para organizar y mantener el lugar de trabajo limpio y ordenado. Las 5S son: Seiri (clasificación), Seiton (orden), Seiso (limpieza), Seiketsu (estandarización) y Shitsuke (disciplina).
- Poka Yoke: Consiste en implementar dispositivos o mecanismos para evitar errores o fallas en la producción.
- Kanban: Es un sistema de control de producción que se basa en la utilización de señales visuales para indicar el momento en que se debe producir o mover un producto.
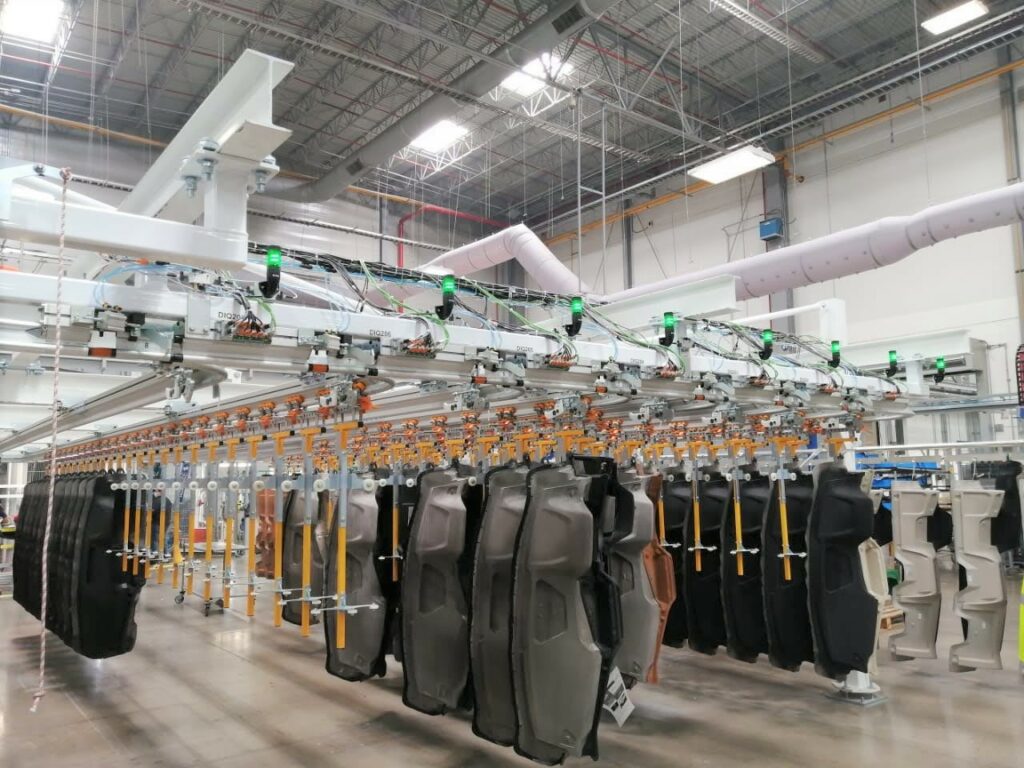
- Just in Time (JIT): Significa producir solo lo que se necesita, en la cantidad que se necesita y en el momento en que se necesita, reduciendo los inventarios y los costos asociados.
- Andon: Es un sistema de señalización visual que indica problemas o interrupciones en la producción.
- Value Stream Mapping (VSM): Es una herramienta para mapear todo el proceso de producción, identificando áreas de desperdicio y oportunidades de mejora.
- Jidoka: Se refiere a la automatización con un toque humano. Implica detener la producción en caso de detectar un problema, para corregirlo y evitar que se repita en el futuro.
- FIFO (First In, First Out): es una técnica de control de inventarios que consiste en consumir los materiales o productos más antiguos primero, para evitar la obsolescencia o el desperdicio de materiales.
Cada herramienta y técnica se utiliza para abordar diferentes áreas de la producción y mejorar continuamente el proceso.
Los desafíos futuros del Lean Manufacturing: ¿Cómo mantener la relevancia en un mundo cambiante?
A pesar de los numerosos éxitos alcanzados por el Lean Manufacturing, la adopción continua de tecnologías disruptivas y los cambios en la forma en que los consumidores compran y los empleados trabajan presentan nuevos desafíos. El futuro del Lean Manufacturing se centrará en tres áreas principales: adaptabilidad, digitalización y sostenibilidad.
La adaptabilidad será clave para el éxito del Lean Manufacturing, ya que las empresas deberán ser capaces de ajustarse rápidamente a los cambios en la demanda del mercado y a la disrupción tecnológica. La flexibilidad y la agilidad serán fundamentales para mantenerse competitivos.
La digitalización también será esencial para el futuro del Lean Manufacturing. Las herramientas y tecnologías digitales, como el Internet de las cosas, el análisis de datos y la inteligencia artificial, podrán ayudar a mejorar la eficiencia y reducir los costos en la producción, así como a mejorar la toma de decisiones.
Por último, la sostenibilidad será un desafío importante para el Lean Manufacturing. Las empresas deberán trabajar para reducir su impacto ambiental y aumentar la eficiencia energética en la producción, así como encontrar maneras de reducir la cantidad de residuos generados.
Para superar estos desafíos, las empresas deben continuar adoptando una mentalidad de mejora continua y estar dispuestas a adaptarse y evolucionar en un entorno empresarial en constante cambio.
Optimización de la logística interna: clave para el éxito del Lean Manufacturing
La logística interna desempeña un papel fundamental en el éxito del Lean Manufacturing. Su objetivo principal es garantizar la entrega de los materiales y componentes necesarios para el proceso de producción en el momento justo y en la cantidad adecuada, evitando así la acumulación de inventario o los cuellos de botella.
Para lograr esto, es necesario aplicar las técnicas y herramientas del Lean Manufacturing, como el mapeo de valor, la producción justo a tiempo y la mejora continua. Además, se deben considerar factores como el diseño de los espacios de almacenamiento, la planificación de rutas y la elección de proveedores confiables.
Algunas de las prácticas que pueden implementarse para mejorar la logística interna en el marco del Lean Manufacturing son:
- Implementar el sistema kanban: un método de gestión de inventario que utiliza señales visuales para indicar cuándo es necesario reabastecer los materiales, como el sistema pick-to-light.
- Aplicar el principio de las 5S: una metodología para organizar el espacio de trabajo y aumentar la eficiencia, que se basa en cinco pilares: selección, orden, limpieza, normalización y disciplina.
- Utilizar la tecnología para el seguimiento de la cadena de suministro: herramientas como los sistemas de identificación por radiofrecuencia (RFID) para un seguimiento en tiempo real.
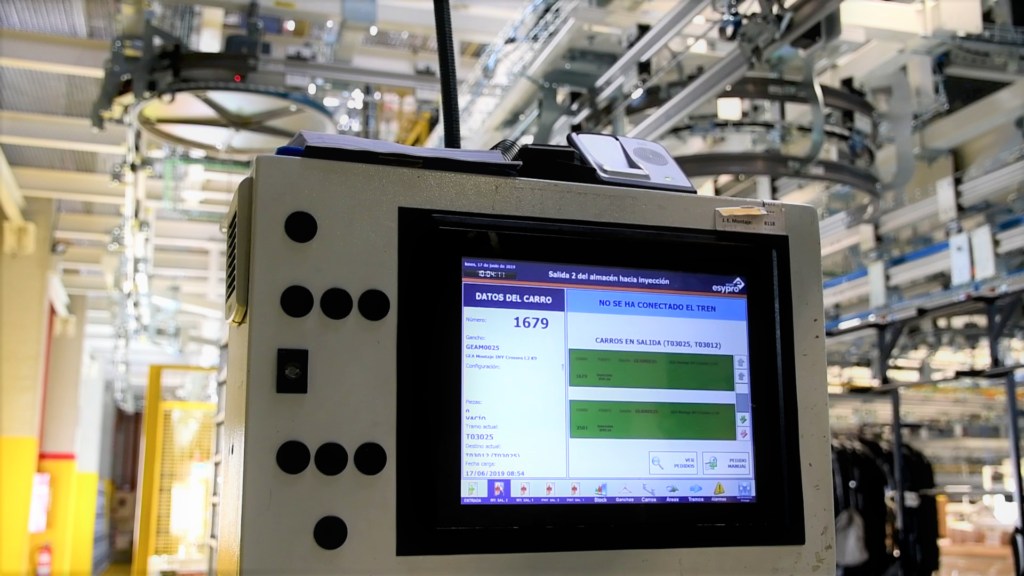
En resumen, la logística interna es una pieza clave en la implementación exitosa del Lean Manufacturing. Al mejorar la eficiencia en la entrega de materiales y componentes, se logra una reducción significativa en los costos de producción y una mejora en la calidad del producto final. Para lograr una logística interna eficiente se recomienda trabajar con expertos en el área, como Esypro, que pueden brindar soluciones personalizadas y eficaces.
Contáctanos y descubre cómo podemos ayudarte a mejorar tu logística interna y llevar tu empresa al siguiente nivel en el Lean Manufacturing.