Lean Manufacturing and material flow are inseparable concepts for improving operational efficiency. In an environment where every movement directly impacts productivity, it’s not enough to implement isolated solutions. It’s essential to adopt a mindset that prioritizes value and eliminates waste at all stages of the process. How can this philosophy be put into practice to transform your material flow? Here’s how.
Material Flow: The Heart of Intralogistics
Material flow refers to the coordinated movement of products, supplies, and components within a plant. It is the axis that connects all stages of the production process. When this flow is inefficient, disruptions, inventory buildup, excessive handling, and hidden costs arise, all of which negatively impact profitability.
Lean Techniques for Optimizing Logistical Flow
The Lean Manufacturing philosophy aims to optimize this flow by applying specific techniques such as:
- Just-In-Time (JIT): Ensures that materials arrive exactly when they are needed, preventing inventory buildup and unnecessary waiting times.
- Kanban: Implements a visual system for managing material flow, facilitating efficient replenishment and preventing overproduction.
- 5S: Organizes and maintains the work environment clean and orderly, improving material access and eliminating unnecessary movements.
- Poka-Yoke: Introduces error-proofing mechanisms to prevent defects in material handling and transport.
- Heijunka: Helps level the workload, ensuring a uniform flow of materials even with demand fluctuations.
At Esypro, we understand that an efficient material flow based on Lean principles is key to competing in demanding markets. That’s why our solutions are designed to optimize this flow, helping reduce costs, increase productivity, and ensure that every movement counts.
Lean Manufacturing Objectives Applied to Material Flow
Efficient intralogistics doesn’t just transport materials; it moves them with purpose. It is key to achieving maximum productivity.
Achieving this level of optimization requires more than just technology. A strategic approach focused on eliminating waste and prioritizing value-generating activities is necessary.
The Lean Manufacturing approach to material flow is crucial for improving productivity. It connects each decision with tangible improvements in efficiency and competitiveness.
Below, we explore how to apply these Lean objectives to intralogistics to overcome operational challenges and improve plant performance.
Reduce Time Waste
In intralogistics, time is an invaluable resource. Every second counts to ensure materials arrive at the right place at the right time.
How can this be achieved? With automated solutions like Esyconveyor, which minimize downtime and guarantee smooth, reliable transport. They also help reduce human errors and improve synchronization between processes.
Visualize Workflow in Real Time
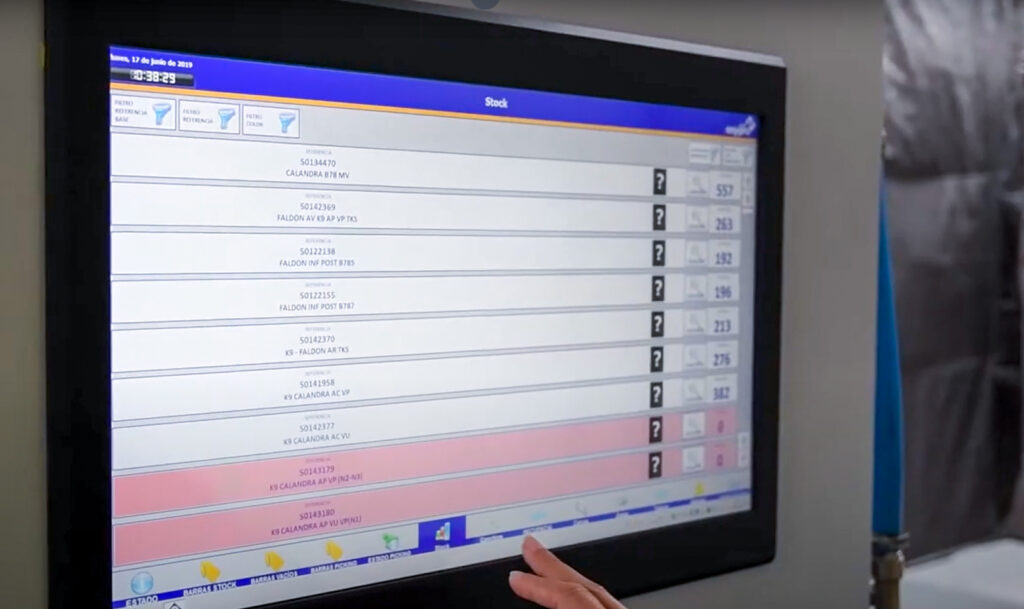
Visibility is key for proactive action. Technologies like Esyair not only store and transport materials but also gather valuable data on cycle times, location, and the status of items. These insights allow you to identify inefficiencies and continuously optimize processes.
Eliminate Bottlenecks
A bottleneck occurs when a process cannot handle the volume of materials it receives, affecting overall flow. Lean Manufacturing suggests balancing process rhythms and strategically managing materials in critical areas. For example, Almaflex is ideal for introducing organized accumulation points in key areas. These temporary buffers allow you to absorb demand spikes or irregularities, ensuring the overall flow remains uninterrupted. The key is adjusting the capacity and rhythm of each stage to maintain a steady, efficient flow.
Encourage Continuous Improvement
Continuous improvement is one of the core pillars of Lean Manufacturing. It’s not about making drastic changes all at once, but rather making small, consistent adjustments that, over time, lead to significant impact. Regularly assessing material flow and associated processes helps identify areas for improvement, reduce waste, and optimize resources. By adopting this approach, your plant not only becomes more efficient but also develops the flexibility needed to respond to demand changes.
Examples of Application: Optimizing Material Flow with Lean Manufacturing
Esypro has implemented projects that embody Lean principles with concrete applications, successfully optimizing material flow:
Integrated Logistics Between Tier 1 and OEM
A major Tier 1 supplier with a global presence faced the challenge of providing bumpers in sequence for two production lines at an OEM in Spain. Although the Tier 1 supplier had the necessary production capacity, they lacked the adequate space and management for storing and preparing parts for the new model.
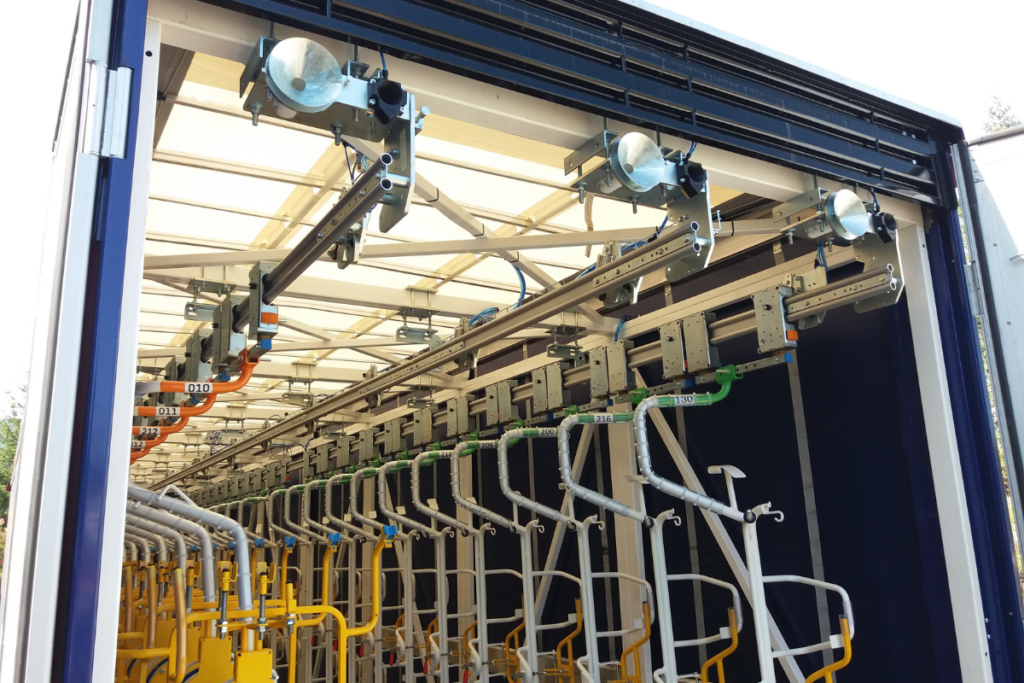
Esypro designed a system based on Esyair that provided an integrated solution:
- Smart storage: Two double-level warehouses were created, utilizing the building’s height for automatic accumulation.
- Flexible sequential work: Capable of feeding 4 parts per minute in JIS for the two line edges.
- Direct transport without packaging: Parts travel suspended from the Tier 1 system directly to the OEM line edge on specialized trucks, eliminating handling and disposable packaging.
- Automated internal logistics: The entire flow, from injection to line edge, is managed with minimal operator intervention, ensuring precision, efficiency, and real-time traceability.
This solution not only addressed storage and management limitations but also allowed the Tier 1 supplier to secure the project and maintain a smooth and efficient material flow.
Implementation of FIFO Warehouses and Pick to Light
In several Tier 1 projects, Esypro implemented FIFO storage systems designed to ensure an orderly and efficient flow. This can be achieved through accumulation bars, where parts are loaded from one end and unloaded from the other, ensuring the correct order.
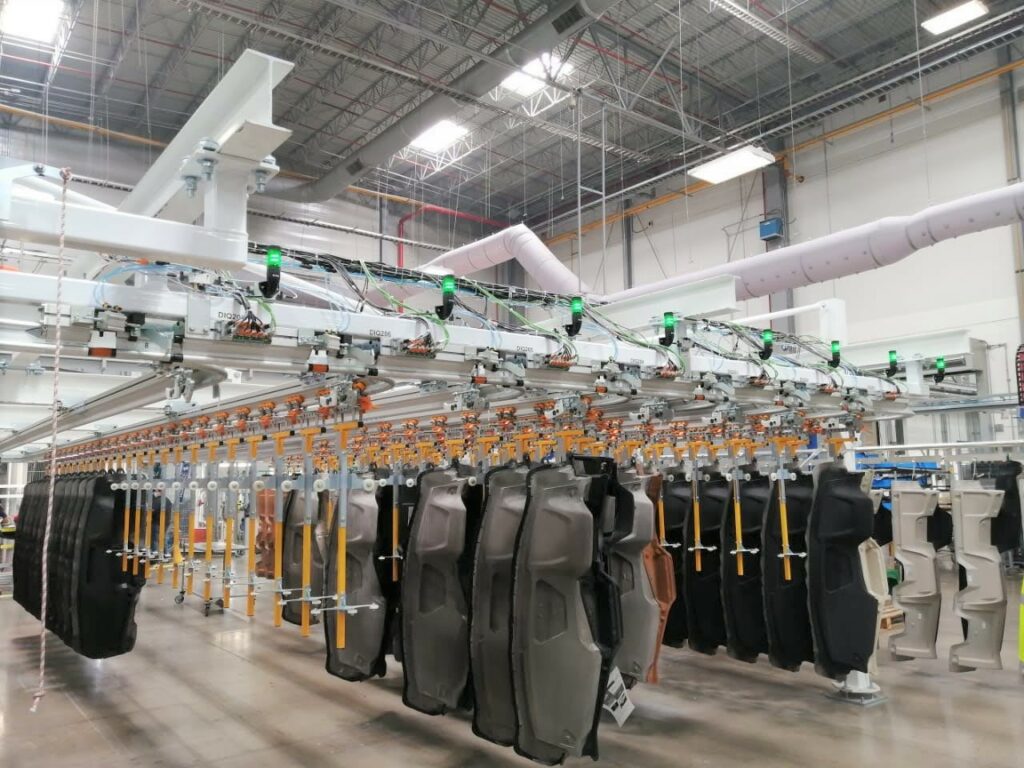
To further enhance efficiency, Pick to Light systems were integrated in some cases. This system guides operators with visual signals, helping them quickly identify the correct bar to load or unload. These simple automations:
- Facilitate operator work, reducing errors.
- Increase operational speed.
- Easily integrate into fully manual systems, improving efficiency without large investments.
This combination of simplicity and functionality reinforces the Lean approach, eliminating waste and optimizing resources.
Maximizing Space in the Plant
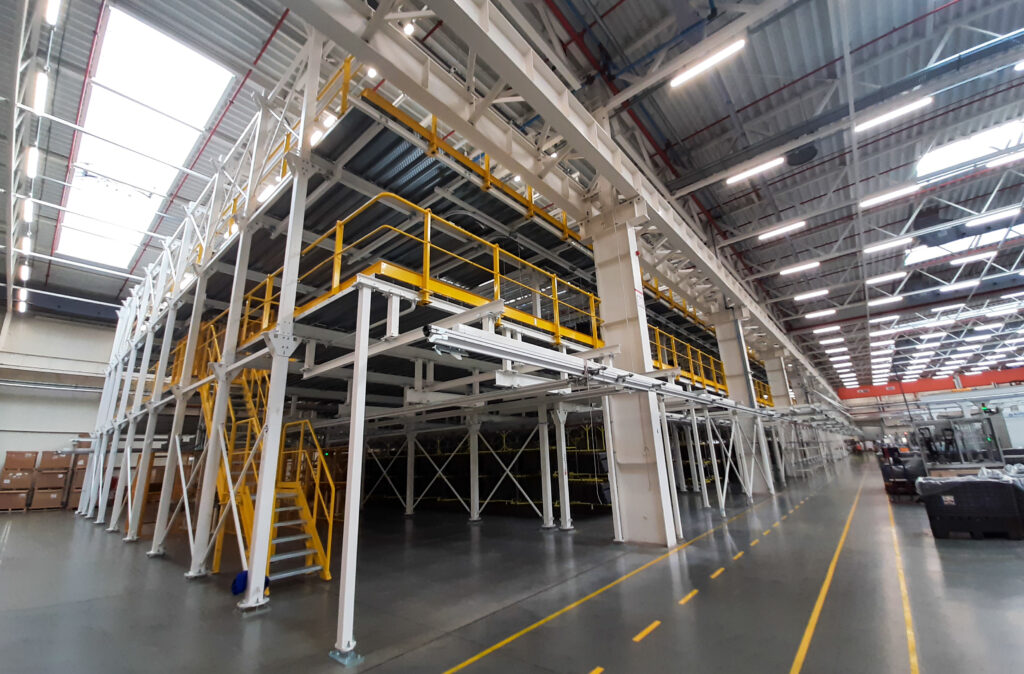
Plants with limited space face constant challenges in handling increased production volumes. To resolve this issue, Esypro often designs solutions that maximize vertical space using pedestrian platforms. These strategies:
- Free up critical floor space, improving mobility within the plant.
- Increase storage capacity without the need for physical expansions.
- Improve material organization, ensuring quick and orderly access.
By optimizing space usage, these solutions allow plants to grow sustainably and efficiently.
Efficient Management of Low-Rotation Parts and Quality Control
In complex warehouses, low-rotation parts present a unique challenge for organization and material flow. Esypro has designed systems that optimize their handling, improve traceability, and ensure availability when needed. These solutions:
- Significantly reduce search times.
- Prevent disorganized accumulation in warehouses.
- Maintain a cleaner, more efficient material flow.
A notable example of this approach is the low runner project we developed for a Tier 1 supplier in the United States. In this case, we freed up floor space with a pedestrian platform, optimizing the handling of low-rotation parts using a double-level storage system with automatic lifts.
Additionally, a small buffer was implemented to conduct quality control without interrupting the production sequence. This buffer allowed technical staff to inspect parts and manage rework of defective items while ensuring material flow remained uninterrupted and operations continued efficiently.
You can read more about this project in this article.
Benefits of Lean Material Flow in Your Plant
Applying Lean Manufacturing principles to material flow has a tangible impact on your operations:
- Increased productivity: Reduces search times and interruptions, improving coordination between areas.
- Cost reduction: Minimizes expenses related to downtime, excessive storage, and rework, while saving energy with automated solutions.
- Adaptability: Our modular solutions adapt to the changing needs of your plant, ensuring a future-proof investment.
- Improved quality: Fewer errors and defects during the production process.
- Increased customer satisfaction: By responding quickly to market demands, you can better meet customer expectations.
Make Lean Manufacturing and Material Flow Your Competitive Advantage
In a market that demands efficiency and speed, implementing Lean Manufacturing in your material flow is not an option; it’s a necessity. At Esypro, we understand that every plant has unique challenges. That’s why we design tailor-made solutions to meet your objectives, combining technology, innovation, and expertise to optimize your operations.
Contact us to discover how we can help you bring your Lean objectives to life.