At the core of every company are individuals whose passion and experience propel innovation and success. At Esypro, we’re fortunate to have visionaries like Antonio Gregores, our Product Manager. With a career distinguished by profound market insight and a dedication to excellence, Antonio has played a pivotal role in shaping the development and advancement of our products. In this exclusive interview, we’ll have the privilege of exploring his vision and gaining insights into the unique perspectives he brings to the solutions we offer at Esypro.
Could you share some highlights of your professional journey that have been crucial to your current role as Product Manager at Esypro?
I’ve been lucky to begin working at a young age, while studying industrial engineering. This early start enabled me to gain experience across diverse sectors and engage with individuals at various organizational tiers. These experiences have deepened my understanding of end-users’ needs, goals, skills, and constraints. Throughout, I’ve maintained ongoing relationships with suppliers and clients, immersing myself in their processes and challenges. Of course, my 18-year tenure in this company, with its diverse roles, has provided unparalleled learning opportunities within the industry.
How has the role of Product Manager been integrated into Esypro and what is its strategic importance for the company?
Having a mature and reliable product is fundamental, and above all, applying it appropriately in different solutions from the earliest stages of any project. We don’t just understand the product as a series of components assembled in one way or another. When a client decides to start a project with us, we work together on specification, planning, development, manufacturing, assembly, commissioning, and operation throughout its lifecycle. From my perspective, the complete customer experience is part of the product delivered. To ensure a successful outcome, it’s essential to have a team that masters all these phases and has the appropriate technical resources to execute them effectively. Achieving this is a challenge in which the Product Manager must actively participate.
What is the process you and your team follow for the development of new products?
I would say that rarely does a product line emerge out of thin air at a precise moment, like an inventor struck with an idea and sketching away on a napkin as if in a trance. Likewise, there isn’t a standardized process based on the clichés of “extensive market research and analysis of customer needs.” There’s a fair bit of storytelling in these narratives.
The product development process typically entails a challenging, often hurried evolution, building upon previous solutions applied in new contexts.
I can give you some examples of development processes that I find interesting:
Incorporating user feedback. It may seem very basic, but the changing environments involving interaction with different types of people lead to the incorporation of many new features, solving new problems, and improving the user experience.
Adopting emerging technologies. We monitor the evolution of technologies involved in our process so that we can seize new opportunities in product evolution, whether to reduce costs and time or to obtain new functionalities and higher levels of quality. Adapting to different markets and social and economic situations.
Adapting our product to different clients in their different locations, with their legislative, cultural particularities, and investment amortization capacities, forces the evolution of the product to adapt to different circumstances. Similarly, the evolution over time of economic and social situations within the same market requires the application of different products and in different ways over time, promoting, for example, changes in automation levels or system flexibility to deal with changing or unstable situations.
What are the distinctive features that make Esypro’s intralogistics systems stand out compared to other market solutions?
In this case, I will answer you with a cliché: what distinguishes Esypro’s systems is the dedication with which our teams engage in them. When this is the case, everything else falls into place effortlessly. While many companies may claim the same, many of them know it’s not always true.
What strategies or methods do you use to effectively identify the real problems and needs of customers, with the aim of improving products?
The best approach is to immerse ourselves in our customers’ processes and gain a profound understanding of their daily challenges. We cultivate a culture of ongoing feedback and continuous monitoring of installed systems throughout their lifecycle. Moreover, customers remain in contact with us for maintenance and facility evolution, providing us with a comprehensive understanding of the outcomes of all our developments over the years.
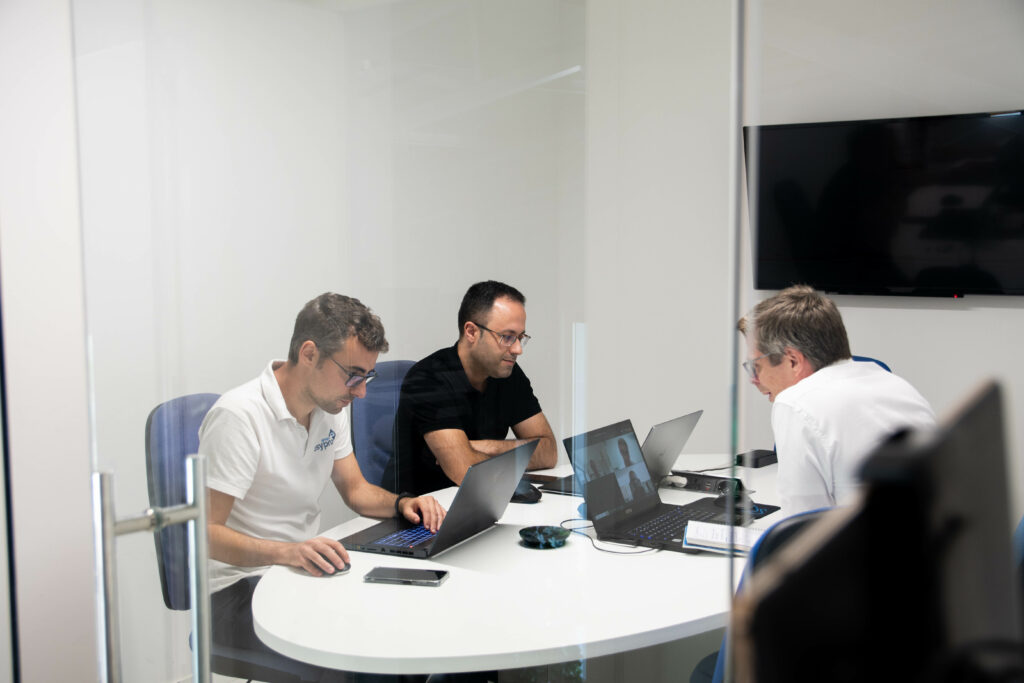
In the context of sustainability and environmental commitment, how does Esypro ensure that its intralogistics solutions are energy efficient and environmentally friendly?
There are several aspects to consider regarding this issue. The most crucial aspect is that our systems are inherently much more efficient than traditional methods. Transporting and storing hanging parts, whether done manually or automatically, is always more energy-efficient than using containers or boxes that require forklifts for handling, with the associated energy consumption. Likewise, careful handling of parts leads to less waste and rework caused by damaged pieces.
However, beyond that phase, we apply certain strategies to further improve this aspect:
We integrate sustainable design principles into our product development process from the outset. Most of our components are made from partially recycled materials and are almost always fully recyclable, such as steel, aluminum, or technical plastics, whether injected or machined. We optimize designs to reduce resource consumption and eliminate waste, prioritizing the use of injected plastic components containing recycled material over machined components that generate waste during production. Additionally, the industry’s move towards sustainability often aligns cost-optimal processes with environmentally friendly practices.
We use components with high energy efficiency and calculate actuators in a way that minimizes energy consumption during operation. Our installed electric motors are top brands and belong to the highest energy efficiency categories available. Similarly, our pneumatic components are of high quality to enhance performance, minimize compressed air losses, and are dimensioned optimally to reduce air consumption.
We optimize our customers’ processes. Our systems facilitate the implementation of intelligent control strategies to optimize transport and sequencing routes. We prioritize minimizing movements of load units and place unused components on standby, ensuring efficient operations for our customers.
Could you mention a specific product from Esypro that exemplifies and reflects the company’s sustainability policies?
Undoubtedly, the best example is the esyair. It is a fully automated system for transporting and storing hanging parts. In addition to the sustainability features mentioned earlier, thanks to the integrated control methods, it allows for many other interesting sustainability-related activities. For instance, we can continuously monitor stock levels and predict future consumption patterns to manage production batches optimally. It facilitates the proactive preparation and delivery of individual parts to customized consumption points, thereby averting returns of incomplete packaging and minimizing space occupancy in production areas. Moreover, it seamlessly integrates with Autonomous Mobile Robots (AMRs) or Automated Guided Vehicles (AGVs) to cover areas inaccessible to overhead conveyors. Additionally, its versatility allows for the integration of manual zones in low-demand areas or the adaptation to specific conditions. Hence, it stands as the quintessential embodiment of a sustainable system.
What is your vision on how the implementation of technologies like artificial intelligence will impact the evolution of industrial logistics systems?
I believe there could be several lines of work. Artificial intelligence has been evolving a lot lately. One of the most well-known fields of AI work, because it’s the closest to the general public right now, is the generation of texts, images, and videos from prompts in natural language. Stated like this, it doesn’t seem to have a great application in our sector in the short term, but natural language recognition may trigger some advances very soon in operator interface systems. After all, many of the operators who interact with our systems already carry a tablet connected to control and monitoring systems, which also has a microphone and speakers or headphones. Surely they can soon be used for interesting purposes.
One of the aspects that I find most interesting is AI’s ability to optimize operations based on system demand and process states. Current algorithms can already analyze large volumes of historical data, production parameters, and stock statuses to do certain things like suggesting actions, optimizing batches, and planning manufacturing. The big challenge right now is to have the necessary data modeled in the right way to feed an AI. It is not possible at the moment to do without the predictions and intuitive decisions of an expert operator. Nevertheless, we already have some background research lines, even if only as assistance to the operator in decision-making regarding production and system maintenance issues, to be prepared and ready to take the leap when the time comes, just as they are doing in medicine, for example, with the diagnosis of certain diseases. In terms of information management and algorithms used, these are things that have more in common than it seems.
Is there any progress you can share about the upcoming developments Esypro is currently working on?
I can tell you that we are making significant progress in the development of esyair. Soon, we will see innovations in the mechanical components that will provide us with new and very interesting functionalities. Additionally, we are also preparing the next generation of control and monitoring software. Updates are guaranteed by the year’s end and into the following one. That’s as much as I can share publicly for now.