When we think of a warehouse, it’s easy to imagine the routine of receiving and shipping orders, the movement of shelves and forklifts. But behind that apparent simplicity lies a complex universe. The art of warehousing goes beyond logistics; it’s a science in itself, filled with tools and strategies designed to minimize costs. Managing the flow of materials is just as important as the production processes; both deserve equal attention. That’s why we offer you some practical tips here that can make a difference.
Layout optimization: Maximum efficiency per square meter
Before making any changes to the layout, it is crucial to conduct a detailed analysis of the available space. This includes measuring the warehouse dimensions, identifying underutilized areas, and evaluating the accessibility of different sections of the warehouse.
The layout design should consider ergonomics and ease of movement for the staff. Travel distances should be minimized, and the arrangement of products and aisles should be optimized to facilitate navigation and access. Many warehouses do not fully utilize the available vertical space. Installing tall shelves and using second levels can help maximize the space.
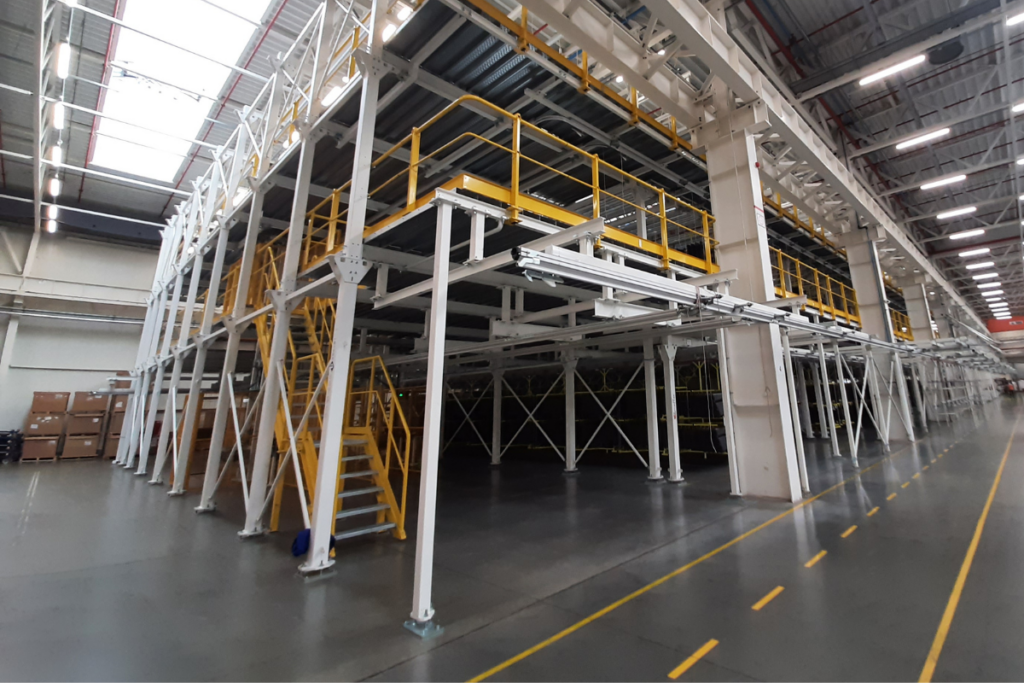
Moreover, in the case of products that store better vertically or hanging, specific storage systems can be used. Overhead systems are ideal for items with an appearance that benefit from being suspended rather than stacked on conventional shelves. These systems allow for easy and quick access to goods, maintaining their integrity and minimizing the risk of damage.
The warehouse layout should be designed with flexibility in mind. Changes in demand, new products, or updates in processes may require adjustments to the layout. Maintaining a modular and easily adaptable arrangement allows for changes to be made without disrupting the warehouse’s normal operation.
Once the new layout is implemented, it’s important to continuously track and evaluate to ensure it’s performing as intended. This includes monitoring operational efficiency, gathering feedback from staff, and making adjustments as necessary to optimize warehouse performance.
Excessive inventory reduction: Optimizing stock management
In warehouse management, reducing excessive inventory is a key strategy to minimize costs and improve operational efficiency. Understanding product demand is crucial to avoid overstocking. Use historical data, market trends, and demand forecasts to adjust inventory levels more accurately.
Implement the Just-in-Time (JIT) system to receive raw materials and produce products just in time to meet customer demand. This reduces the need for large inventories and minimizes storage costs. Additionally, use inventory management software to monitor stock levels in real-time and establish automatic reorder points. This allows you to maintain optimal inventory levels without excess or shortage.
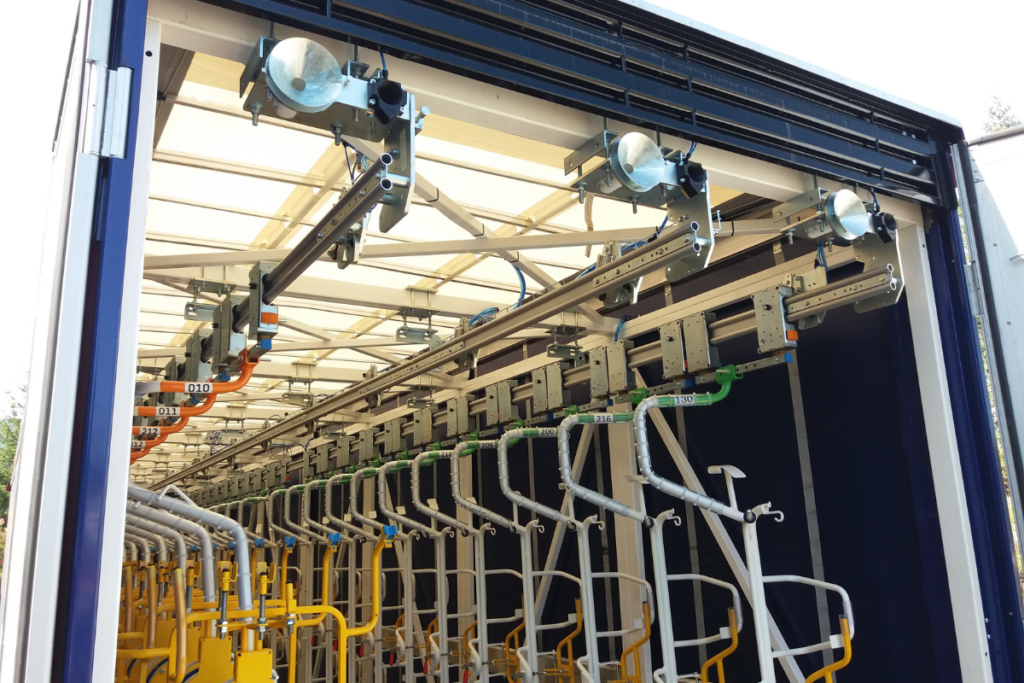
Establish strong relationships with your suppliers and work collaboratively to improve delivery accuracy and reduce lead times. This allows you to maintain lower inventories without compromising product availability. Implement inventory rotation policies to ensure that older products are sold first. This prevents obsolescence and reduces the need for discounts to clear out old products.
Conduct regular inventory audits to identify obsolete, expired, or damaged products. Removing these items from inventory frees up space and reduces storage costs. Take advantage of negotiation opportunities with suppliers to secure volume discounts on your purchases. This enables you to maintain lower inventories without increasing the unit costs of products.
Technological innovation: Warehouses 4.0
Integrating technology into your warehouse operations can result in significant long-term cost reductions. Warehouse Management Systems (WMS) are essential for optimizing processes, minimizing errors, and providing real-time inventory data. While the initial implementation may involve an investment, the long-term benefits in terms of efficiency and waste reduction are substantial.
WMS offers a range of functionalities, from order management to inventory tracking. This allows for greater accuracy and control in all warehouse operations. Additionally, consider technologies like Radio-Frequency Identification (RFID), which streamlines inventory tracking and reduces product search times. RFID technology enables real-time monitoring of products as they move through the warehouse, improving efficiency and minimizing errors.
Another area of technological innovation that can be beneficial is robotics. Robots can automate repetitive manual tasks, such as picking and packing orders, increasing productivity and reducing labor costs.
Integrating advanced technology like Esyair into your warehouse operations can result in cost reductions and a notable improvement in operational efficiency. Esyair is an overhead conveyor system with accumulation bars, controlled by real-time software. It is designed to optimize the flow of materials and products within the warehouse.
The real-time software control provides complete visibility of the flow of materials and products in the warehouse, allowing for more precise and efficient management of operations. Additionally, Esyair is compatible with autonomous transport systems such as AMRs (Autonomous Mobile Robots) and AGVs (Automated Guided Vehicles). This allows for seamless integration with other cutting-edge technologies in the warehouse.
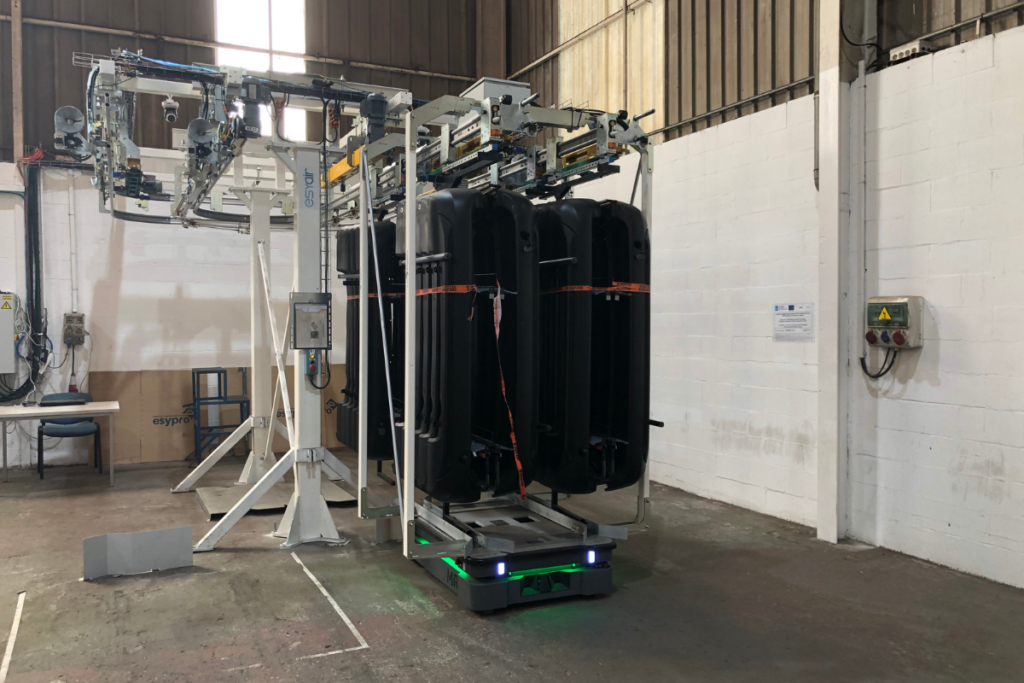
Talent development: Building a well-trained team
Investing in staff training might seem like an additional expense when trying to reduce costs. However, the reality is that a well-trained team is an invaluable asset for any warehouse. Proper training not only improves operational efficiency but also reduces costly errors and fosters a safer, more productive work environment.
Focus on training your team to perform multiple functions within the warehouse. A versatile and skilled team can better adapt to fluctuations in demand and reduce the need for temporary staff during peak periods. Additionally, increased training can promote staff retention, as employees value opportunities for growth and professional development.
Regular training updates are essential to keep your team up-to-date with the latest best practices and emerging technologies. The constantly evolving warehouse environment requires employees to stay informed about new tools and processes to maintain efficiency and competitiveness. Moreover, continuous training can enhance team morale and motivation, leading to increased productivity and long-term reductions in operational costs.
In summary, staff training is a strategic investment that can yield significant benefits for your warehouse. By enhancing your team’s skills and knowledge, you are building a solid foundation for your business’s future success, promoting a culture of excellence and continuous growth.
Implementing Lean Tools: Fostering a culture of continuous improvement in the warehouse
When we think of Lean, it is common to associate it primarily with production, such as in Lean Manufacturing. However, it is crucial to understand that Lean principles have a much broader scope and can be effectively applied in other areas, including warehouse management and logistics in general. Extending Lean to the warehouse environment involves implementing various tools and techniques aimed at improving operational efficiency, reducing costs, and optimizing processes throughout the supply chain.
In this regard, applying Lean methodologies in warehouses becomes a key strategy for companies seeking to maximize productivity and minimize waste in their logistics operations. For example, process standardization, space organization (using the 5S methodology), and material flow optimization (through Kanban) are fundamental practices that can transform warehouse efficiency.
Additionally, Lean tools such as identifying and eliminating waste (Muda), focusing on workplace safety (integrating 5S with safety practices), and promoting respect for people in the workplace not only improve operational performance but also help create a safer, more collaborative, and motivating work environment.
Moreover, aspects like implementing regular meetings to review operational status and discuss improvement opportunities (such as Asaichi meetings), level production to avoid work peaks and minimize waiting times, and fostering a culture of continuous improvement are central to the Lean philosophy and can significantly impact the efficiency and competitiveness of a warehouse.
Towards Sustainability: Promoting environmentally responsible practices
The integration of sustainable and environmentally friendly practices into warehouse operations not only benefits the planet but can also result in significant cost savings and improvements in operational efficiency.
A key strategy to achieve this is energy optimization. In addition to measures such as using LED lighting and installing motion sensors, incorporating photovoltaic panels to harness solar energy can significantly reduce dependence on conventional energy sources, thereby decreasing electricity costs and contributing to carbon emissions reduction.
Furthermore, proper waste management, including recycling programs, not only reduces costs associated with waste disposal but can also generate additional income through the sale of recyclable materials.
Sustainable transportation is another important area to consider, where load consolidation and the use of low-emission vehicles can reduce fuel costs and greenhouse gas emissions.
Eco-friendly packaging can not only reduce long-term costs but also improve brand image by demonstrating a commitment to environmental sustainability.
Similarly, efficient water management, through the installation of low-flow devices and water reuse in cleaning processes, can generate significant savings in water and sewage costs.
Finally, warehouse space optimization, by implementing vertical storage systems and reducing unnecessary inventory, can decrease the need for costly expansions and improve operational efficiency.
By adopting these sustainable practices, warehouses can not only reduce their environmental impact but also improve their operational efficiency and reduce long-term costs, while promoting responsible business practices and enhancing their reputation in the market.
Finding trusted partners: Building strategic relationships
Collaborating with trusted partners can be a determining factor for success in warehouse process optimization. By establishing strong relationships with suppliers, carriers, and other key players in the supply chain, opportunities arise to reduce costs and improve operational efficiency.
When selecting partners, it is crucial to prioritize service quality, consistency in service delivery, and transparency in business relationships. With reliable partners, the risks associated with delivery delays, order errors, and other setbacks that could increase operational costs are minimized.
Furthermore, close collaboration with partners can foster innovation and continuous improvement. Through the exchange of knowledge and best practices, opportunities to optimize processes, reduce waste, and increase efficiency throughout the supply chain can be identified.
In summary, seeking and establishing relationships with reliable partners can be a key strategy to drive competitiveness and long-term success for your warehouse.
Esypro: Your global partner for Warehouse Optimization
When it comes to optimizing warehouse processes, Esypro stands out as your trusted strategic ally. With a solid track record and a customer-centric approach, Esypro offers intralogistics solutions designed to enhance efficiency and reduce costs in storage operations.
We not only provide a wide range of high-quality products, such as overhead conveyor systems (Esyconveyor) and both manual (Almaflex) and automatic (Esyair) overhead warehouses, but we also offer personalized service and exceptional technical support. Our expert team is committed to understanding each client’s unique needs and providing tailored solutions that drive business success.
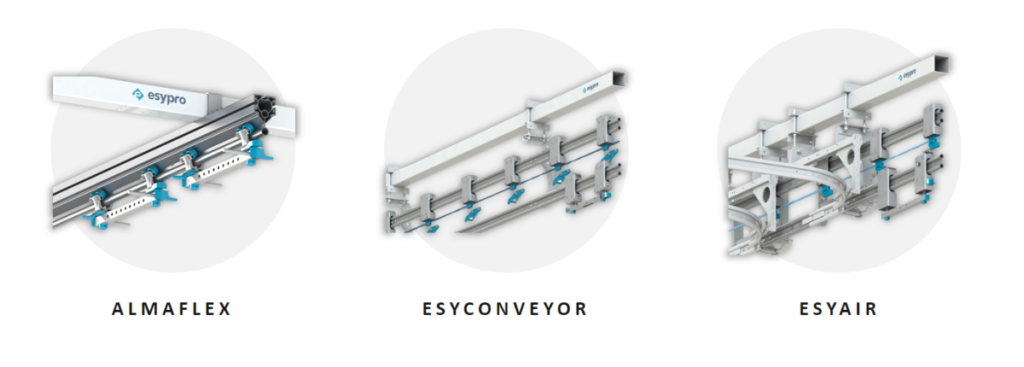
By choosing Esypro as your partner in warehouse intralogistics management, you can trust that you’ll have access to cutting-edge technology, proven solutions, and a committed team ready to help you achieve your business goals. Take the next step in optimizing your warehouse with Esypro!