In the industrial world, especially in the automotive sector, overhead conveyors play a crucial role in intralogistics and production efficiency. However, like any equipment, they require specific safety and maintenance measures to operate optimally and safely. In this article, we will address the fundamental safety aspects you need to consider when implementing and maintaining an overhead conveyor system, ensuring not only the protection of your workforce but also the maximization of operational efficiency.
Training: The fundamental pillar of safety
Proper training of personnel is essential to ensure the safety and efficiency of overhead conveyors. Maintenance and operational teams must be well-trained to handle the system correctly and respond effectively to emergency situations.
Comprehensive training is key: the team should receive thorough instruction on the system’s operation, safety procedures, and proper use of personal protective equipment (PPE). Additionally, this training should be ongoing, with regular updates to incorporate new procedures and regulations.
Including simulations and regular practice sessions helps staff become familiar with potential issues and respond quickly and effectively. This not only improves safety but also optimizes system performance, increasing operational efficiency and reducing downtime.
In summary, investing in staff training ensures a safer and more productive work environment, maximizing the performance of overhead conveyors and minimizing associated risks.
Essential steps for commissioning an overhead conveyor
Before starting any Esyconveyor system, you must perform a series of checks to ensure safe and efficient operation. Here are the essential steps to follow:
1. Visual inspection of the structure
Begin by visually inspecting the conveyor structure. Ensure there are no deformations or damages incurred during assembly. A well-maintained structure is fundamental for the safe operation of the system.
2. Component check
Verify that all functional components are operational. This includes stop stations, drag modules, and elevators. Ensure each part is in optimal condition and functioning according to the manufacturer’s specifications.
3. Load unit verification
Use the verification gauge to confirm that the load units have no deformations. Additionally, ensure that loading and unloading operations are carried out smoothly, especially when performed automatically with robots or handlers.
4. Air pressure
Check that the air pressure in the system is adequate, which should be 6 bar. Incorrect pressure can affect the system’s performance and safety.
5. Safety systems
Ensure that all safety systems, such as emergency stop buttons and torque controls, are functioning correctly. These systems are essential to prevent accidents and handle emergency situations.
6. Detection and sensors
Verify that all sensors and detection systems are operational. Accurate detection is key to avoiding failures and ensuring the system responds appropriately to operating conditions.
7. Cinematic chain tension
Check that the tension of the rope is correct. Inadequate tension can cause issues in the conveyor’s operation.
8. Dynamic test
Perform a dynamic test by passing all load units at least once through the loading and unloading stations. This helps identify any operational problems and ensures the system runs continuously and efficiently.
9. Cycle time verification
Finally, verify that the actual cycle time and cadence match the established specifications. This ensures the system meets operational and production requirements.
Safety guidelines for secure operations
To ensure a safe environment when using overhead conveyors, follow these guidelines:
Restricted access
Limit access to the facility to authorized and properly trained personnel only. This ensures that only those who are familiar with the safety procedures can operate or intervene in the system.
Maintenance with system stopped
Perform all maintenance tasks with the system completely stopped. In exceptional cases where it is necessary to work with the system in motion, only visual inspections in designated areas are allowed.
Safe circulation
Always use the designated walkways and avoid invading the transit areas of the Load Units. It is prohibited to pass under the conveyor tracks, except in specifically designated areas.
Operations in designated areas
Operations with transported pieces should be carried out only in designated areas, always with the load unit stopped and stabilized at loading or unloading points.
Adequate protection
Use appropriate personal protective equipment (PPE) and always maintain collective and individual protection measures. This includes wearing helmets, goggles, gloves, and other safety elements according to the task.
Maximum authorized load
Do not exceed the maximum authorized load of 200 Kg/m² on work platforms. Respecting this limit is crucial to avoid structural damage and ensure system stability.
Clothing and accessories
Avoid wearing loose clothing or items that can get caught in the conveyor’s moving parts. This minimizes the risk of accidents and injuries.
Do not tamper with systems
Do not tamper with or disable detection or control systems, as this could create risks for both personnel and equipment. Safety systems must always be operational.
Emergencies
In case of malfunction, use the emergency stop button to immediately halt the system. Do not restart until the issue has been identified and resolved.
Working at heights
When working at heights, use safety harnesses and establish a safety perimeter on the ground to protect people from falling objects.
Welding and pneumatic maintenance
During welding work, protect platforms with fire-resistant cloth to prevent the spread of incandescent projections. For pneumatic maintenance, ensure the main valve is closed to prevent unintended actuator movements.
These measures are crucial to prevent accidents and ensure the safe and efficient operation of overhead conveyor systems.
Safety measures for overhead conveyors
Ensuring safety in the use of overhead conveyors is essential to protect both people and equipment. The selection of appropriate safety measures will depend on various factors, such as the installation design and specific environmental needs. Below are the main safety measures that should be chosen based on the characteristics of each system:
Emergency stop buttons
These devices should be strategically and accessibly located. When activated, emergency stop buttons immediately halt the equipment, allowing for a rapid response in case of anomalies or dangers. It is crucial to ensure that the system is not restarted until the problem has been resolved.
Safety barriers
Barriers control access to areas with automatic movements and stop the system if someone attempts to enter these zones. Their necessity depends on the risk associated with the areas they protect and the system design.
Perimeter fencing
These prevent unauthorized access to the installation and may include sensors that stop operation if restricted areas are breached. The choice of perimeter fencing depends on the system layout and the need to protect specific areas.
Safety gates
These gates prevent access to dangerous areas and only allow opening when it is safe. They stop the automatic operation of the system when opened, which is vital in high-risk areas.
Safety mats
Located in critical areas, safety mats halt the system if stepped on. They are essential in platforms where access to dangerous areas must be strictly controlled.
Signage
Signs with pictograms and warnings should be placed at entrances and key areas to provide clear indications about safe access. Proper signage is fundamental to ensure personnel follow necessary precautions.

Not all these measures will be necessary in every installation; the selection will depend on the layout, specific risks, and operational needs of each system. At Esypro, we work to advise and implement the most suitable safety solutions for each case, ensuring a safe and efficient work environment.
Preventive maintenance: Key to durability and safety
We recommend a preventive maintenance program designed to optimize the performance and durability of your overhead conveyors. This approach not only prevents unexpected failures but also ensures a safe and efficient work environment. Here are our recommendations for effective preventive maintenance for Esyconveyor:
Annual maintenance
- Structural inspection: Verify that the conveyor structure shows no deformations or damages that could affect its operation.
- Component check: Ensure that all essential components, such as stop stations, drag modules, and elevators, are in good working condition.
- Condition of the running tracks: Check that the running tracks and the tension of the cinematic chain are appropriate to avoid blockages and operational failures.
- Cleaning and lubrication: Perform a thorough cleaning using recommended degreasers and lubricate the moving parts to ensure smooth operation and reduce wear.
Semi-annual maintenance
- Cleaning brushes inspection: Examine the cleaning brushes and replace them if necessary to maintain system efficiency.
- Load unit check: Ensure that the load units and the spacing between trolleys meet the recommended specifications to avoid blockages and ensure a continuous flow.
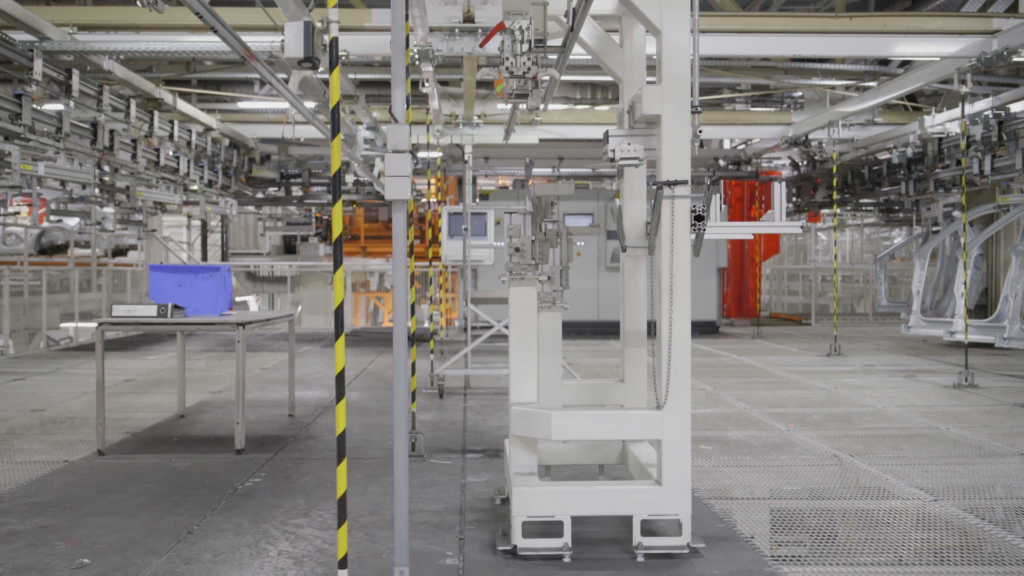
Implementing this preventive maintenance program, as recommended for Esyconveyor, is key to ensuring the optimal performance of your overhead conveyors and prolonging their lifespan. Keep a detailed record of all inspections and repairs for proactive and effective management.
Esypro: Commitment to excellence and safety
At Esypro, we are dedicated to enhancing your operations with overhead conveyor solutions that prioritize safety and efficiency. With Esyconveyor, you can trust that your overhead conveyor system will be in the best hands, optimized to deliver exceptional performance at every stage of the process.
For more information about our products and services, feel free to contact us. We are here to help you take your production plant to the next level with Esyconveyor.