In recent years, the global automotive industry has had to adapt to a series of unprecedented disruptions that have tested the resilience of supply chains. Factors such as the COVID-19 pandemic, geopolitical tensions, shortages of key components, and drastic demand fluctuations have revealed how vulnerable international logistics networks can be. In this changing landscape, concepts like resilience and nearshoring—the relocation of suppliers or processes closer to home—have gained prominence.
Companies, including Original Equipment Manufacturers (OEMs) and their Tier 1 suppliers, are reevaluating their logistics strategies with a clear objective: to mitigate risks and maintain operational continuity, without completely sacrificing the efficiency required by Lean models.
Recent disruptions affecting the supply chain
Over the past five years, the global supply chain has suffered multifaceted shocks:
Impact of the COVID-19 pandemic
The 2020 global health crisis exposed the fragility of many supply chains. Simultaneous lockdowns in multiple countries led to factory shutdowns, international transport restrictions, and labor shortages. Beyond halting production at origin, the pandemic caused severe demand swings, making planning difficult and creating bottlenecks that lasted for months. For many industrial companies, it was the first major warning that a global disruption can simultaneously affect every link in the chain—from manufacturing to final delivery.
Semiconductor shortages in production
A modern car may contain between 1,400 and 3,000 electronic chips. The semiconductor supply interruption since 2020 impacted over 169 industrial sectors, with the automotive sector being hit especially hard. It’s estimated that this shortage cost the global automotive industry around $210 billion in revenue in 2021 alone, due to millions of vehicles that couldn’t be produced. Manufacturers were forced to halt assembly lines, revealing the lack of buffer stock for such a critical component.
Geopolitical tensions
The war in Ukraine in 2022 worsened supply chain crises. Ukraine had been a supplier of wiring harnesses and other low-cost but essential components, and their absence forced temporary shutdowns in European plants. Additionally, Russia and Ukraine are key sources of raw materials. Disruption of strategic inputs exposed excessive dependency on unstable regions. This is compounded by trade tensions between the U.S. and China, which have led to technological restrictions and a push for “friendshoring“—sourcing from allied countries—motivated by both economic and national security concerns.
Logistics crisis and transportation challenges
Disruptions were not limited to input shortages but also affected transportation. In 2021, incidents like the Suez Canal blockage exacerbated delays, and ocean freight rates hit record highs (multiplying by 4 or 5 times pre-pandemic rates) due to port congestion and container imbalances. Many companies with distant suppliers faced unpredictable lead times and had to resort to urgent measures (costly air freight, last-minute changes) to avoid production stoppages.
Tariffs and new trade tensions
In April 2025, the United States announced a general 10% tariff on most imports as part of a strategy to reduce the trade deficit and encourage domestic production. The measure also includes higher additional tariffs for certain countries with which the U.S. has significant trade imbalances. Following reactions from some nations and warnings from various industrial sectors about the potential impact of these measures, the administration decided to pause their implementation for 90 days for most countries, with a few exceptions. During this reprieve, many companies are accelerating stockpiling to hedge against possible cost increases if the tariffs go into effect. Others are rethinking their entire supply chain.
These situations have made one thing clear: efficiency alone is not enough. A supply model optimized solely for lowest cost (e.g., relying on a single overseas supplier) can fail spectacularly in the face of unexpected events. Hence the importance of building resilient supply chains, capable of absorbing shocks.
The return of nearshoring: Relocating to build resilience
In response to this volatility, many companies are looking to strengthen the resilience of supply chains by reconsidering where they source their key materials and components.
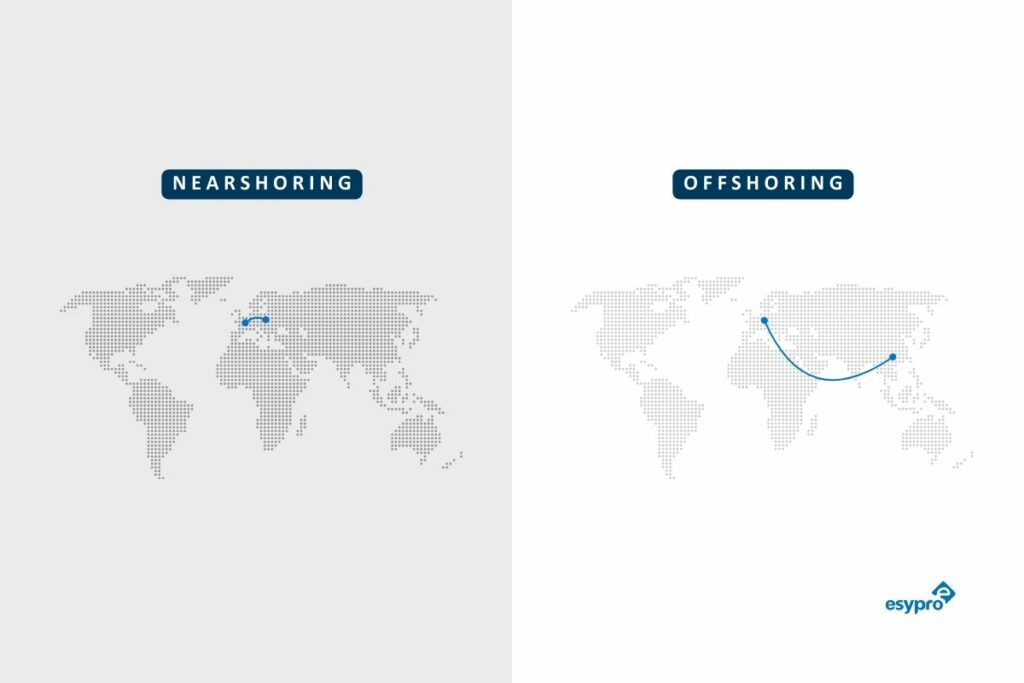
Nearshoring—bringing processes or suppliers closer to the final market—is back on the table for several reasons:
- Reduced distance and faster response time: Shortening the supply chain (e.g., replacing an Asian supplier with one in the same region, whether North America or Europe) reduces transit times and exposure to disruptions at distant ports or borders. A nearby supplier can, in theory, restock in days instead of weeks, allowing better reaction to demand changes or unforeseen events.
- Lessons from the pandemic: Industry studies indicate that after the pandemic, over 60–70% of manufacturing firms evaluated adjustments to their supply base, including regional relocation. Some automotive OEMs have outlined strategies to “regionalize” their production.
- Stability and compliance: Nearshoring is also driven by stability considerations. Companies seek environments with lower risks of sudden tariffs, export restrictions, or border closures. In nearby regions, it is easier to align quality, labor, and intellectual property standards. For example, a European manufacturer may have better control and more frequent visits to a supplier in Eastern Europe than one in the Far East, improving collaboration and reducing compliance risks.
It’s important to note that nearshoring is not a one-size-fits-all solution. Relocating the supply chain involves costs and depends on the destination region’s technical capabilities and scale. In some cases, dependency on a specific country cannot be eliminated overnight. Each company must balance cost savings versus risk: the “optimal” decision will depend on context, product, and strategy.
From globalization to nearshoring
The shift toward closer, more resilient supply chains is having a direct impact on industrial intralogistics.
Many companies have moved from strict Just-in-Time models to more hybrid approaches, holding some safety stock to provide a buffer against disruptions. Nearshoring allows companies to recover parts of the original JIT model, leveraging supplier proximity and better real-time demand visibility.
Operationally, a shorter supply chain means more frequent deliveries in smaller batches. This demands more flexible logistics layouts, agile material reception, and the ability to reconfigure internal flows without halting production.
In sectors like automotive, the Just-in-Sequence (JIS) model benefits from nearshoring: sequenced parts arrive from nearby suppliers directly to the production line, even transported pre-hung and in order, replacing traditional warehousing with a fast and precise system.
To manage this complexity with agility, many companies are adopting digital planning and traceability tools. These allow them to adjust production in real time and respond to delays without shutting down the factory.
How to reinforce the resilience of supply chains
There’s no universal solution for building the resilience of supply chains, but several effective practices can be applied depending on the context:
Multiple sources and development of local suppliers
Instead of relying on a single global supplier for a given component, OEMs are qualifying alternative suppliers in different regions. Some have helped smaller local suppliers scale up technologically, integrating them into their supply chains. This doesn’t mean abandoning trusted global partners but rather having contingency plans. A bonus from diversification is encouraging competition and potentially reducing long-term costs, even if short-term investments are needed to certify new suppliers.
Maintaining strategic inventory
Without returning to past excesses, many companies are defining which components warrant safety stock and how much. For example, chips, wiring harnesses, and special bearings—parts with long lead times or high risk—justify a few weeks of coverage in inventory. Conversely, bulky items that are easy to source locally might still be managed with minimal stock. This hybrid strategy (“Just-in-Time” in general, but “Just-in-Case” for critical parts) aims to balance cost with protection. As analysts warn, every bad inventory decision has a cost: excess stock ties up capital and space, while insufficient stock can halt production. Resilience means fine-tuning that balance.
Extended chain collaboration
Trust and open communication with suppliers and third-party logistics providers become essential. Some companies have formed joint rapid-response teams with their main Tier 1s, meeting regularly to analyze risks (e.g., monitoring geopolitical, health, or climate indicators) and adjust plans. They also share demand forecasts more frequently—moving from monthly to weekly or even daily projections—so that every link in the chain can prepare ahead. This close collaboration builds a “cushion” of resilience without overloading each link with resources.
Innovation in intralogistics
A more robust supply chain needs internal logistics that can adapt quickly to change. Operational innovation is key here. Some plants are adopting transport and storage systems that reduce handling and optimize space. They also create intermediate buffers and allow continuous feeding of JIT or JIS flows, even from nearby suppliers.
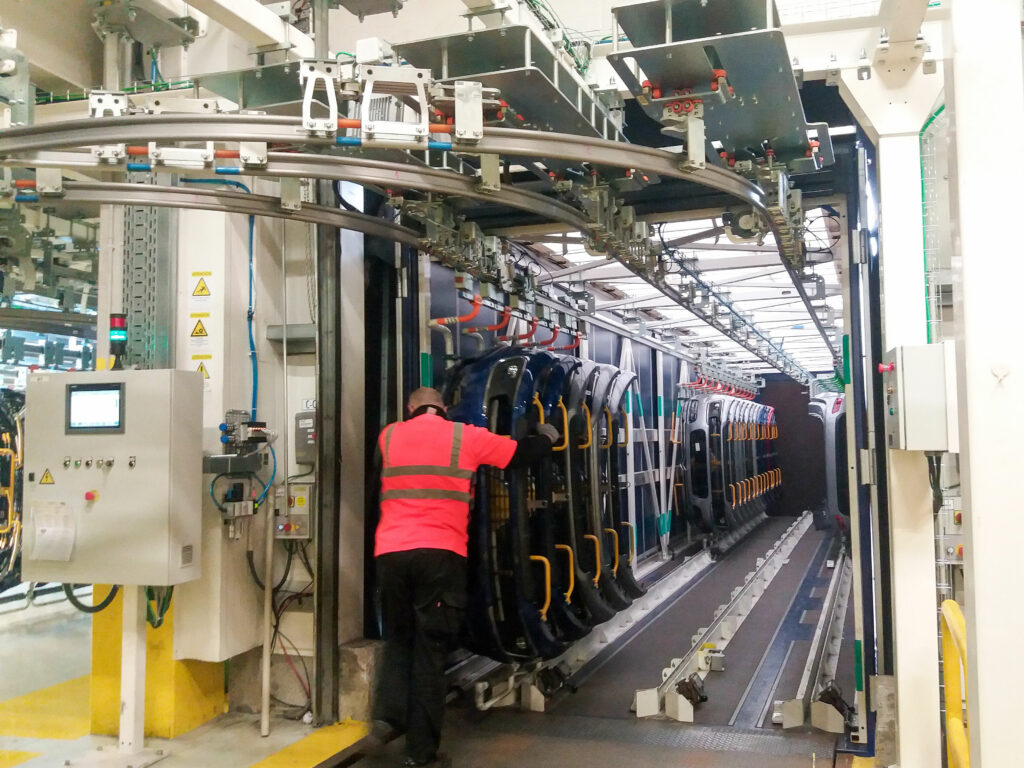
For example, in several industrial facilities developed by Esypro, systems have been implemented where parts arrive hung, sequenced, and ready to enter the line directly from the truck, with no intermediate plant storage. In these cases, internal and external intralogistics function as a single, fluid unit: transportation systems—already integrated from the supplier—replace the traditional warehouse and enable faster adaptation to variability.
Understanding the context to strengthen the chain
The pursuit of resilience in the automotive supply chains (and other industrial sectors) reflects a hard-earned lesson: extreme optimization must give way to robustness and flexibility. Strategies such as nearshoring, combined with adjustments in intralogistics and planning processes, can enhance a plant’s ability to keep operating in changing environments. However, there is no one-size-fits-all solution. Each company must assess its specific context—product type, location, cost structure, risk tolerance—before deciding how much to relocate, how much extra inventory to hold, or what new practices to adopt.
The industry’s overall tone is one of cautious adaptation: diversify without duplicating costs unnecessarily, innovate in internal logistics to gain room for maneuver, and empathize with plant teams facing daily uncertainty. In the end, resilience is not about building invulnerable supply chains (that’s impossible), but about creating supply chains that can absorb shocks and recover quickly.
In summary, strengthening supply chain resilience requires a comprehensive approach—from global sourcing strategy to local intralogistics operations. The goal is that when the next disruption inevitably comes, the response won’t be panic and paralysis, but a rapid, coordinated action.