In 2023, Esypro collaborated with a leading Tier 1 company in the USA, specializing in the manufacturing of automotive bumpers, looking for a new conveyor system. We had a clear goal: to transform their storage management and quality inspection processes. With our solutions, such as Esyconveyor Power & Free and Almaflex, we improved two key areas: low runner storage and piece quality control.
In this article, we show you how our systems helped a client optimize their operation. This allowed them to free up space and ensure a more efficient workflow.
Overhead pre-inspection conveyors: Smooth workflow
In automotive manufacturing, quality is crucial to meet the industry’s high standards. Implementing a pre-inspection system ensures that only approved parts reach the assembly line, avoiding delays and reducing waste.
To achieve this, Esypro installed two Esyconveyor Power & Free circuits: one for front bumpers and one for rear bumpers. Both systems are designed to handle up to 51 hooks per conveyor, operating on a 60-second cycle time. This allows for continuous and efficient inspection of the plant’s 14 bumper references, minimizing downtime in case of rework.

Inspection close to the loading point
The process begins before the piece is integrated into the conveyor. Near the loading station, a trained operator visually inspects each bumper for defects before hanging it on the hook. This initial verification is crucial. It helps identify and separate any piece that doesn’t meet quality standards, ensuring only optimal bumpers enter the sequence.
Once the bumper is inspected and approved, the operator hangs it on an empty hook stopped at a station. To start the process, the operator pulls a cord, which triggers a series of automatic checks. The system verifies the bumper’s presence and reads its label to ensure it’s in the correct sequence. If the information is correct and there’s space in the next station, the hook is released and moves forward. If the label doesn’t match or there’s an error, the hook stops. In this case, the operator must intervene using the HMI (Human Machine Interface).
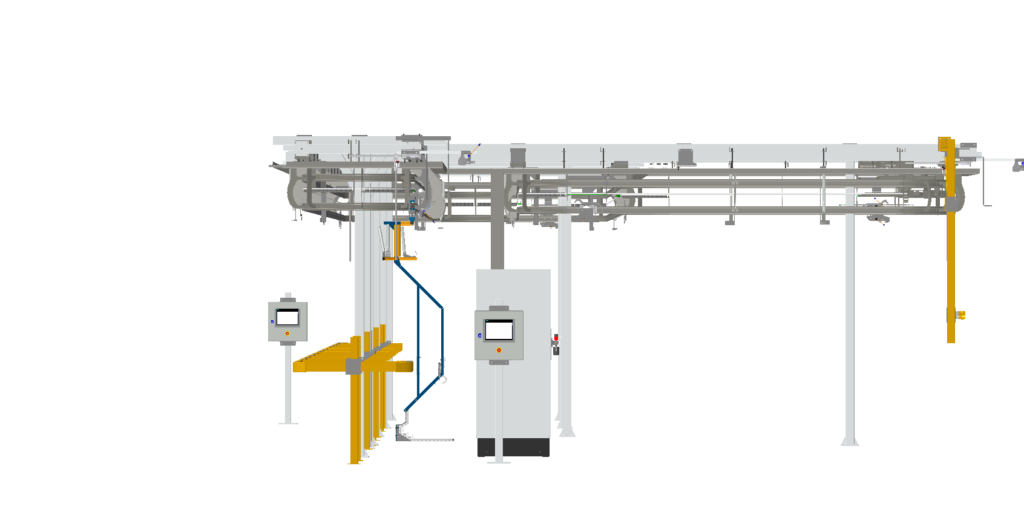
Re-entry station: Completing the sequence
These conveyors also include a re-entry station, designed to ensure that parts needing rework rejoin the flow in a controlled way. At this station, after loading the repaired bumper, the system re-scans the hook’s label to confirm the part is in the correct sequence. If the label is correct, the hook is automatically released and moves to the next stage. If the label is incorrect or the part is missing, the hook stops at the station until the operator manually validates it using the HMI.
Unload station: Controlled order
The final stage in this pre-inspection area is the unload station. Here, the bumper that passed the visual inspection stops automatically for the operator to remove it. After removing the piece, the operator pulls the cord again to validate the system, ensuring an empty hook is available to restart the cycle.
RFID technology for error-free operation
The integration of RFID technology in the pre-inspection system is crucial for ensuring a continuous and error-free flow. The RFID system automatically detects when a sequence of parts is complete, allowing them to advance without manual intervention. This automation helps operators focus on tasks that add real value, such as quality inspection, making the process faster and more reliable.
Low runner storage: Freeing up space with functional solutions
In automotive production, low runner parts present a particular challenge. These are parts used less frequently in the assembly process and are not required continuously. However, they are essential for specific orders or at certain production times. Despite their low demand, storing them takes up significant space in the warehouse. This can cause congestion and limit the ability to manage higher-rotation items.
To solve this problem, Esypro designed a system that strategically reorganizes the warehouse. It uses an elevated platform and the Almaflex system to maximize vertical space without compromising accessibility.
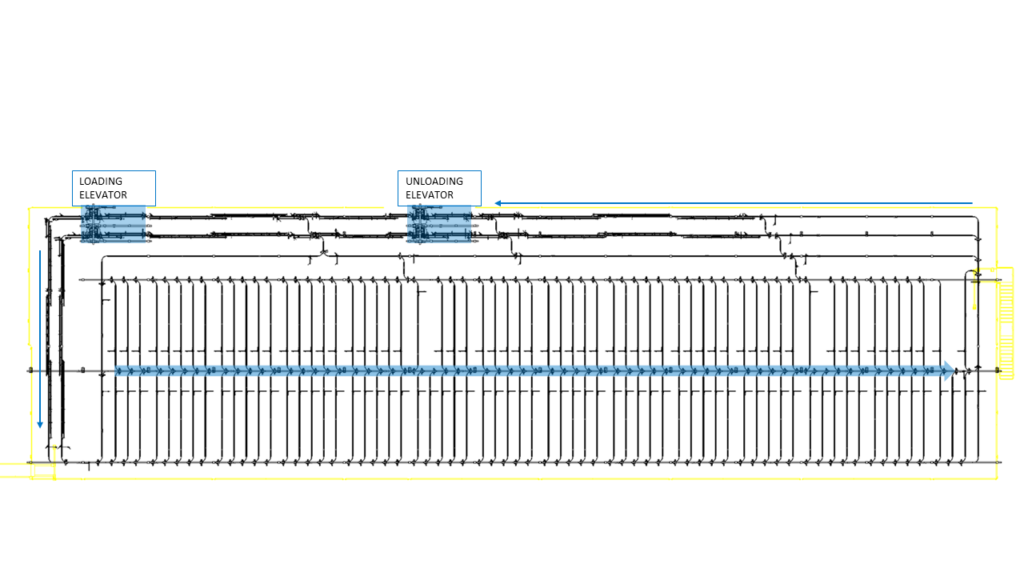
Maximizing vertical space
Esypro’s solution was to install an elevated pedestrian platform that freed up floor space in the plant. This created a specific area for storing low runner bumpers. This approach reduced congestion in work areas and allowed the plant floor to be dedicated to higher-rotation operations, improving the overall efficiency of the warehouse.
On the platform, an Almaflex system was installed, facilitating the manual storage and retrieval of bumpers. It leverages the available height without requiring complex structural changes. The movement of parts between levels is handled by two elevators: one for loading and one for unloading. Both have small automated storage areas on the upper level. Automatic pushers move hooks to and from the elevator, eliminating the need for manual intervention in this part of the process.
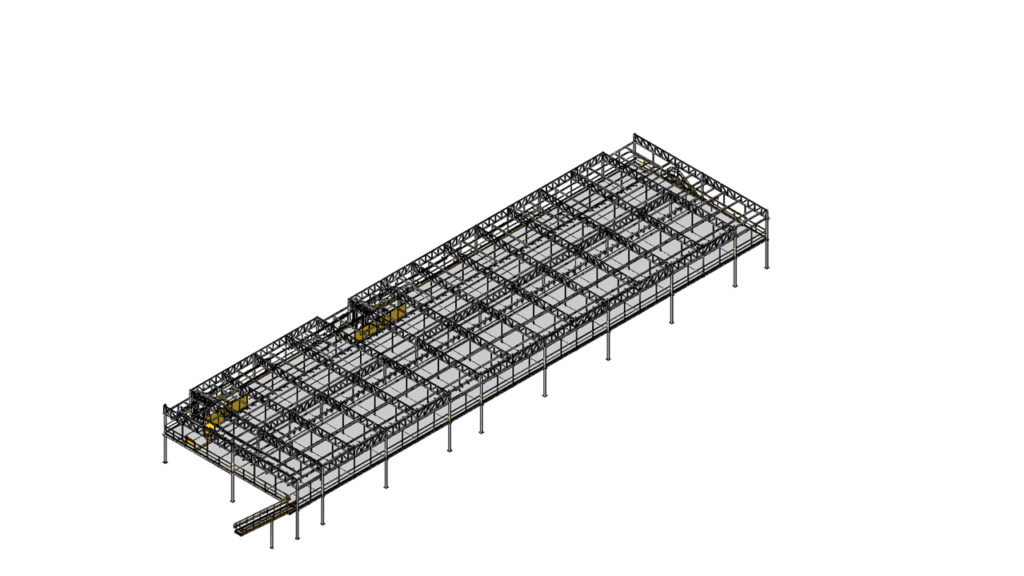
Efficient loading and empty hook buffer
The loading process begins on the lower level. An operator places a low runner bumper on the loading elevator after an empty hook descends automatically from the upper level.
Once the hook is loaded with a bumper, the elevator transports it to the second level. There, another buffer facilitates the transition to the storage system. This automated process maintains a continuous workflow, preventing staff from wasting time on repetitive tasks or waiting for system availability.
It’s important to mention that there’s a small buffer of empty hooks before the loading elevator. This ensures that there are always enough hooks available for loading. The hooks are automatically pushed to the elevator.
Storing in accumulation bars
From the buffer after the elevator, an operator moves the hooks with parts to the accumulation bars of the Almaflex system. These bars are designed to organize bumpers in an accessible and orderly way. They have double switches at their ends, making it easier to load parts. The operator directs the hook to the correct bar, ensuring each type of bumper is properly stored.
When a specific bumper is needed, the operator removes the hooks from the opposite end of the accumulation bars and adds them to a sequence headed for the unload elevator. This operation takes place in a central aisle between both storage fronts. In that aisle, the operator uses triple switches to select the correct reference and add it to the sequence.
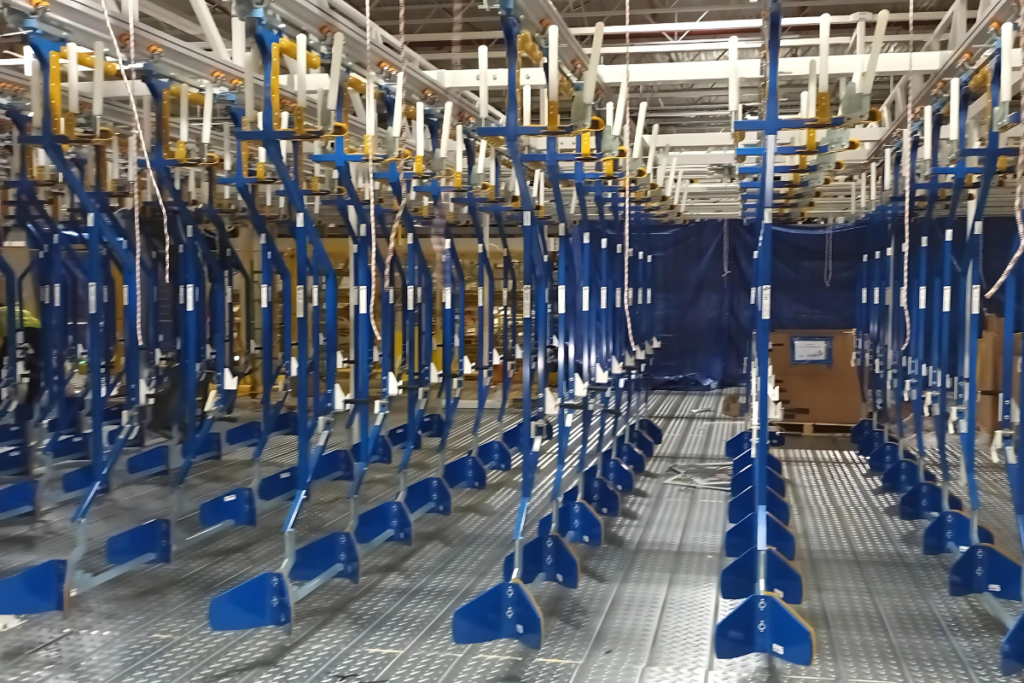
Organized unloading with shortcuts
Once the sequence is complete, the loaded hooks gather in a small buffer before the unload elevator. Automatic pushers transport the hooks to the elevator, which lowers the parts to the lower level, where another operator retrieves them. Meanwhile, the empty hooks return to the system, ready to be reused.
For urgent parts that cannot wait for the regular sequence to reach the unload point, a Fast Line was implemented. This allows the operator to manually send a specific part through a quick path, bypassing the regular flow and ensuring its immediate availability.
Integration and process synchronization
The Almaflex system and elevators integrate efficiently with the human workforce, creating a perfectly synchronized workflow. This reduces unnecessary movements and ensures that parts are available exactly when needed, avoiding bottlenecks and maximizing the operation’s agility. Moreover, the system’s flexibility allows it to adapt to changing storage needs, making it ideal for plants requiring continuous inventory management adjustments.
Results: Efficient solutions that deliver satisfaction
The impact of these solutions was immediate. Our client achieved more efficient organization in their warehouse, eliminating congestion that could disrupt the workflow. The implementation of the vertical storage system not only freed up critical floor space but also improved accessibility to low runner parts, allowing for a quicker response to production demands.
The installation of the pre-inspection buffers ensured seamless quality control, preventing defective parts from advancing to the final production stages. Not only were errors reduced, but the work of the staff was also optimized, integrating an orderly and sequenced material flow.
The most notable aspect of this case is that everything was accomplished without adding unnecessary complexity. Esypro’s solutions are designed to integrate smoothly into existing operations, enhancing performance without interrupting production. The client was fully satisfied with the impact of these changes, observing a significant transformation in their plant’s efficiency.
Simplicity and efficiency in every project
This case demonstrates how Esypro tackles industrial challenges with a focus on simplicity and efficiency. Through the implementation of systems like Esyconveyor and Almaflex, we not only optimize space utilization but also improve operational processes and workflows. Our philosophy is clear: practical solutions that solve real problems and deliver tangible results.
In every project, we tailor our solutions to meet each client’s specific needs. If you’re looking to transform your plant’s operations, don’t hesitate to contact us.