En los últimos años, la industria automotriz global ha tenido que adaptarse a una serie de disrupciones sin precedentes que han puesto a prueba la resiliencia en la cadena de suministro. Factores como la pandemia de COVID-19, tensiones geopolíticas, escasez de componentes clave y variaciones drásticas en la demanda revelaron cuán vulnerables pueden ser las redes logísticas internacionales. Ante este escenario cambiante, conceptos como resiliencia y nearshoring —la relocalización cercana de proveedores o procesos— han ganado protagonismo.
Las empresas, por ejemplo los fabricantes de automóviles (OEMs) y sus proveedores de nivel 1 (Tier 1), están reevaluando sus estrategias logísticas con un objetivo claro: mitigar riesgos y mantener la continuidad operativa, sin sacrificar del todo la eficiencia que exigen los modelos Lean.
Algunas disrupciones recientes con impacto en la cadena de suministro
En los últimos cinco años, la cadena de suministro global ha sufrido choques multifacéticos:
Impacto de la pandemia de COVID-19
La crisis sanitaria global de 2020 puso en evidencia la fragilidad de muchas cadenas de suministro. Los confinamientos simultáneos en múltiples países provocaron cierres de fábricas, restricciones en el transporte internacional y escasez de mano de obra. Además de paralizar la producción en origen, la pandemia generó una fuerte oscilación en la demanda de productos, dificultando la planificación y provocando cuellos de botella que se prolongaron durante meses. Para muchas empresas industriales, fue el primer gran aviso de que una disrupción global puede afectar simultáneamente todos los eslabones de la cadena, desde la fabricación hasta la entrega final.
Falta de semiconductores en la cadena de producción
Un coche moderno puede incorporar entre 1.400 y 3.000 chips electrónicos. La interrupción en el suministro de semiconductores desde 2020 afectó a más de 169 sectores industriales, y en automoción resultó especialmente costosa. Se estima que esta escasez le costó a la industria automotriz mundial unos 210.000 millones de dólares en ingresos solo en 2021 debido a millones de vehículos que no pudieron fabricarse por falta de componentes clave. Los fabricantes se vieron obligados a parar líneas de montaje, evidenciando la falta de stock de seguridad para un componente crítico.
Tensiones geopolíticas
La guerra en Ucrania en 2022 agravó la crisis de suministros. Ucrania era proveedora de arneses de cableado y otros componentes de bajo coste pero vitales; su ausencia forzó paradas temporales en plantas europeas. Además, Rusia y Ucrania son fuentes clave de materias primas. La interrupción de insumos estratégicos expuso la dependencia excesiva de regiones inestables. A esto se suman las tensiones comerciales entre EE. UU. y China, que han llevado a restricciones tecnológicas y a un impulso de “friendshoring” (buscar proveedores en países aliados) por motivos tanto económicos como de seguridad nacional.
Crisis logística y retos en el transporte
La disrupción no solo provino de la escasez de insumos, sino también del transporte. En 2021, incidentes como el bloqueo del Canal de Suez acentuaron retrasos, y los fletes marítimos alcanzaron tarifas récord (multiplicando por 4 o 5 las tarifas pre-pandemia) debido a la congestión portuaria y desequilibrios en contenedores. Muchas empresas con proveedores lejanos experimentaron plazos de entrega impredecibles y necesidad de recurrir a medidas urgentes (fletes aéreos costosos, cambios de última hora) para evitar detener la producción.
Aranceles y nuevas tensiones comerciales
En abril de 2025, Estados Unidos anunció la imposición de un arancel general del 10% sobre la mayoría de las importaciones, como parte de una estrategia destinada a reducir el déficit comercial y fomentar la producción nacional. La medida incluye también aranceles adicionales más altos para ciertos países con los que el gobierno estadounidense mantiene desequilibrios comerciales. A raíz de las reacciones de algunos países y las advertencias de distintos sectores industriales sobre el impacto potencial de estas medidas, la administración decidió pausar su aplicación durante 90 días para la mayoría de los países, con algunas excepciones. Durante esta tregua, muchas empresas están acelerando la adquisición de stock para anticiparse a posibles aumentos de costes si los aranceles finalmente entran en vigor. Otras empresas se están replanteando completamente su cadena de suministros.
Estas situaciones han dejado una lección clara: la eficiencia por sí sola no basta. Un modelo de suministro ultra ajustado al coste más bajo (por ejemplo, depender de un solo proveedor al otro lado del mundo) puede fallar estrepitosamente ante eventos inesperados. De ahí surge la importancia de construir cadenas de suministro resilientes, capaces de absorber shocks.
El regreso del nearshoring: relocalización para ganar resiliencia
En respuesta a esta volatilidad, muchas empresas buscan fortalecer la resiliencia en la cadena de suministro, reconsiderando dónde obtienen sus materiales y componentes clave.
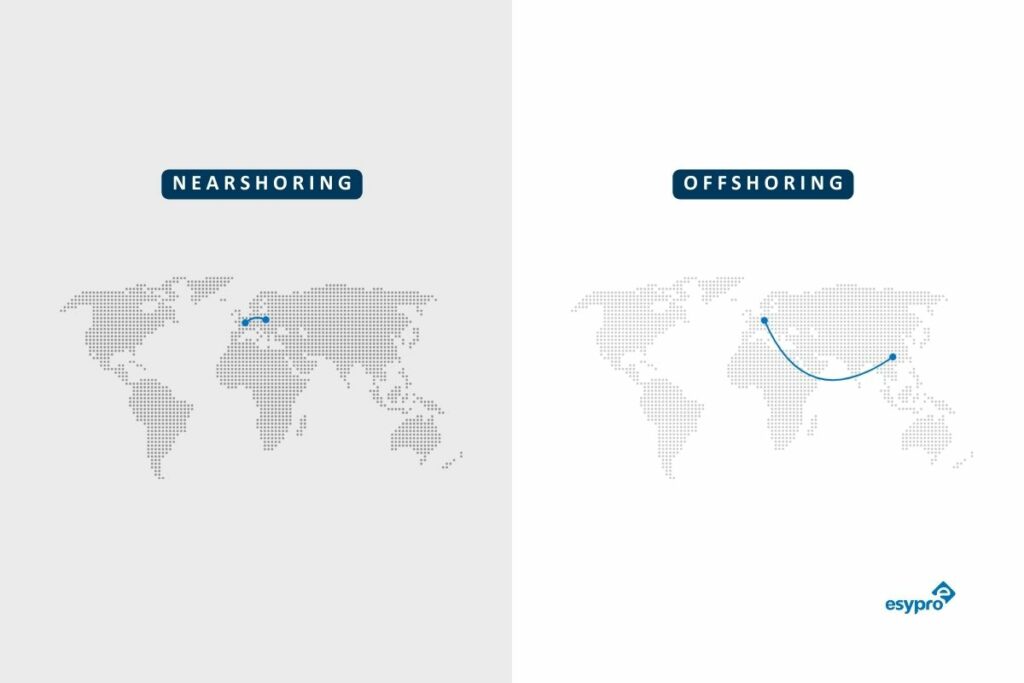
El nearshoring –traer procesos o proveedores más cerca del mercado final– está nuevamente sobre la mesa por varias razones:
- Reducción de la distancia y tiempo de respuesta: Acortar la cadena (por ejemplo, cambiar un proveedor asiático por otro dentro de la misma región, sea Norteamérica o Europa) disminuye los tiempos de tránsito y la exposición a interrupciones en puertos o fronteras lejanas. Un proveedor cercano puede, en teoría, reabastecer en cuestión de días en vez de semanas, permitiendo reaccionar mejor a cambios de la demanda o imprevistos.
- Lecciones de la pandemia: Estudios del sector señalan que tras la pandemia más del 60-70% de las empresas manufactureras evaluaron ajustes en su base de suministro, incluyendo relocalización regional. Algunas OEM automotrices han planteado estrategias para “regionalizar” su producción.
- Estabilidad y cumplimiento: Nearshoring también se ve potenciado por consideraciones de estabilidad. Las empresas buscan entornos con menor riesgo de aranceles sorpresivos, restricciones de exportación o cierres fronterizos. Además, en regiones cercanas es más fácil alinear estándares de calidad, laborales y de propiedad intelectual. Por ejemplo, un fabricante europeo puede tener más control y visitas más frecuentes a un proveedor en Europa del Este que a uno en el Extremo Oriente, facilitando la colaboración y reduciendo riesgos de incumplimiento.
Es importante notar que el nearshoring no es una solución universal. Reubicar la cadena tiene costes e implica asegurar que la región de destino tenga la capacidades técnicas y escala adecuadas. En ciertos casos, la dependencia de un país concreto no se puede eliminar de la noche a la mañana. Cada empresa debe balancear ahorro de costes vs. riesgo: la decisión “óptima” dependerá del contexto, producto y estrategia.
De la globalización al nearshoring
La transición hacia cadenas de suministro más cercanas y resilientes está teniendo un impacto directo en la intralogística industrial.
Por un lado, muchas empresas han pasado de un modelo Just-in-Time estricto a enfoques más híbridos, acumulando cierto stock de seguridad para ganar margen ante imprevistos. El nearshoring permite recuperar parte del JIT original, apoyándose en la proximidad del proveedor y en una mejor visibilidad de la demanda compartida en tiempo real.
A nivel operativo, una cadena más corta implica entregas más frecuentes y en lotes menores. Esto exige layout logísticos más flexibles, recepción ágil de materiales y capacidad para reconfigurar flujos internos sin interrumpir la producción.
En sectores como la automoción, el modelo Just-in-Sequence (JIS) se ve favorecido por el nearshoring: piezas secuenciadas llegan desde proveedores cercanos directamente a línea, incluso transportadas ya colgadas y ordenadas, sustituyendo así el almacén tradicional por un sistema ágil y preciso.
Para gestionar esta complejidad con agilidad, muchas compañías están incorporando herramientas digitales de planificación y trazabilidad. Así ajustan la producción en tiempo real y reaccionan ante cualquier retraso sin detener la fábrica.
¿Cómo reforzar la resiliencia en la cadena de suministro?
No existe una solución universal para lograr una resiliencia sólida en la cadena de suministro, pero sí un conjunto de prácticas efectivas según el contexto:
Múltiples fuentes y desarrollo de proveedores locales
En vez de depender de un único proveedor global de cierto componente, los OEM están calificando proveedores alternativos en regiones distintas. Algunos han ayudado a escalar tecnológicamente a proveedores locales más pequeños, integrándolos en su cadena de suministro. Esto no significa abandonar a los socios globales de confianza, sino tener planes de contingencia. Un beneficio adicional de esta diversificación es fomentar la competencia y potencialmente reducir costes a largo plazo, aunque en el corto plazo implique invertir recursos en homologar nuevos proveedores.
Mantener inventarios estratégicos
Sin volver a los excesos de épocas pasadas, muchas empresas están definiendo qué componentes merecen stock de seguridad y cuánto. Por ejemplo, chips, arneses electrónicos, rodamientos especiales –piezas con largo plazo de reposición o riesgo alto– justifican tener unas semanas de cobertura en almacén. En cambio, piezas voluminosas y fáciles de obtener localmente quizás puedan seguir con inventario mínimo. Esta estrategia híbrida (“Just-in-time” en general, pero “Just-in-case” en lo crítico) busca equilibrar costes con protección. Como advierten analistas, cada mala decisión de inventario tiene un coste: exceso de stock inmoviliza capital y espacio, mientras stock insuficiente puede detener producción. La resiliencia exige afinar ese balance.
Colaboración en la cadena extendida
La confianza y comunicación abierta con proveedores y logística tercerizada se vuelve fundamental. Algunas compañías han establecido equipos conjuntos de respuesta rápida con sus principales Tier 1: se reunen frecuentemente para analizar riesgos (ej. monitorear indicadores geopolíticos, sanitarios, climáticos) y ajustar planes. También comparten proyecciones de demanda más frecuentemente –pasando de pronósticos mensuales a semanales o diarios– para que todos en la cadena puedan anticiparse. Esta colaboración estrecha crea un “colchón” de resiliencia sin tener que sobrecargar a cada eslabón con recursos.
Innovación en intralogística
Una cadena de suministro más robusta necesita una logística interna capaz de adaptarse a cambios con rapidez. Aquí, la innovación operativa es clave. Algunas plantas están adoptando sistemas de transporte y almacenaje que reducen la manipulación y optimizan el espacio. También crean buffers intermedios y permiten una alimentación continua en JIT o JIS, incluso desde proveedores cercanos.

Por ejemplo, en varias instalaciones industriales realizadas por Esypro, se han implementado sistemas en los que las piezas viajan colgadas, secuenciadas y listas para entrar directamente a línea desde el camión, sin necesidad de almacenamiento intermedio en planta. En estos casos, la intralogística interna y externa actúan como una única unidad fluida: los sistemas de transporte —ya integrados desde el proveedor— sustituyen al almacén tradicional y permiten absorber la variabilidad con mayor agilidad.
Entendiendo el contexto para fortalecer la cadena
La búsqueda de resiliencia en la cadena de suministro automotriz (y en otros sectores industriales) refleja un aprendizaje duro: la optimización extrema debe ceder espacio a la robustez y flexibilidad. Estrategias como el nearshoring, combinadas con ajustes en procesos de intralogística y planificación, pueden reforzar la capacidad de una planta para seguir operando ante entornos cambiantes. No obstante, no hay soluciones universales. Cada empresa debe evaluar su contexto específico –tipo de producto, localización, estructura de costes, tolerancia al riesgo– antes de decidir cuánto relocalizar, cuánto inventario extra mantener o qué nuevas prácticas adoptar.
El tono general en la industria es de prudente adaptación: diversificar sin duplicar costes innecesariamente, innovar en logística interna para ganar margen de maniobra, y empatizar con los equipos en planta que lidian día a día con la incertidumbre. Al final, la resiliencia no se trata de construir cadenas de suministro invulnerables (eso es imposible), sino de lograr cadenas de suministro capaces de absorber golpes y recuperarse rápidamente.
En resumen, fortalecer la resiliencia en la cadena de suministro requiere un enfoque integral: desde la estrategia de abastecimiento global hasta la operativa intralogística local. El objetivo es que ante la próxima disrupción (que, tarde o temprano, llegará), la reacción no sea pánico y parálisis, sino una respuesta ágil y premeditada que mantenga las líneas en marcha.