La optimización de la logística interna es clave para aumentar la eficiencia operativa, reducir costes y mejorar la competitividad en entornos industriales. Sin embargo, muchas empresas aún mantienen prácticas obsoletas en intralogística que frenan su crecimiento y provocan pérdidas económicas difíciles de detectar a simple vista.
¿Tu empresa podría estar enfrentando estas ineficiencias sin saberlo? A continuación, te mostramos 7 prácticas comunes que están afectando a tu planta y cómo solucionarlas.
1. Gestionar el inventario con Excel
Aunque Excel ha sido una herramienta útil durante décadas, hoy es una de las prácticas más obsoletas en intralogística, especialmente si buscas trazabilidad y control en tiempo real.
¿Por qué es un problema?
- No ofrece actualizaciones en tiempo real.
- Es propenso a errores humanos.
- No permite trazabilidad automatizada.
- Se vuelve ineficiente a medida que la empresa crece.
¿Cómo optimizarlo?
- Implementa un Sistema de Gestión de Almacenes (WMS) que permita actualizaciones en tiempo real.
- Integra tecnología RFID o códigos de barras para un control preciso del stock.
- Digitaliza tus operaciones con herramientas diseñadas para logística industrial.
2. Mover materiales con montacargas en rutas ineficientes
Muchas empresas dependen de montacargas o incluso del transporte manual de materiales dentro de la planta. Aunque estas soluciones pueden parecer económicas, pueden estar ralentizando la producción sin que te des cuenta.
¿Por qué es un problema?
- Aumenta los tiempos de traslado.
- Genera más tráfico y posibles accidentes en planta.
- No aprovecha bien el espacio disponible.
¿Cómo optimizarlo?
- Implementa transportadores aéreos en segundos niveles para liberar espacio en el suelo.
- Incorpora AGVs (vehículos autónomos guiados) para optimizar el flujo de materiales.
- Diseña circuitos logísticos más eficientes con herramientas modulares.
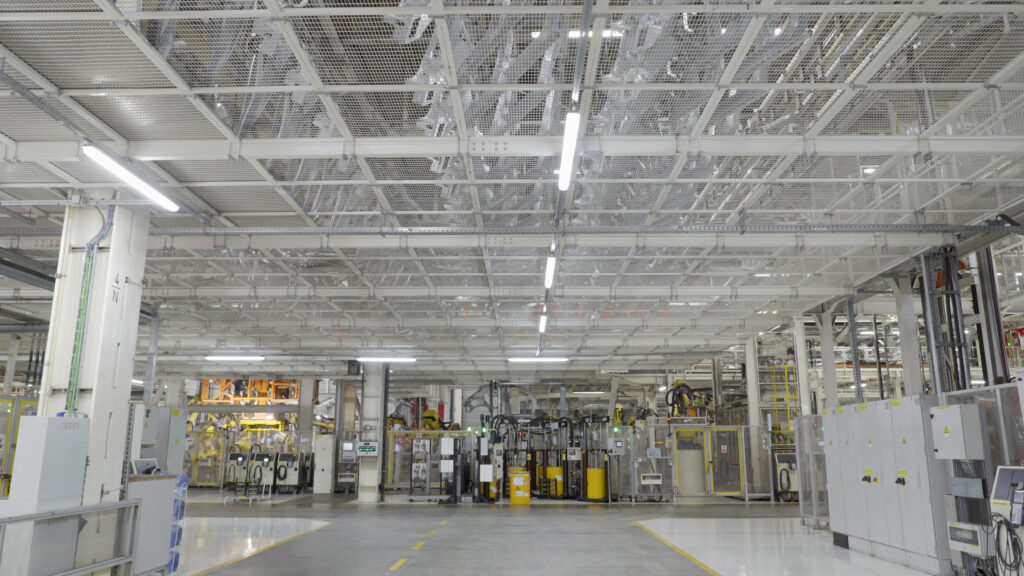
3. Picking desordenado
El picking es una de las tareas más críticas en un almacén. Si todavía se realiza de manera manual y sin optimización, los errores y los retrasos en la preparación de pedidos son inevitables.
¿Por qué es un problema?
- Se pierde mucho tiempo buscando productos.
- Aumentan los errores en la preparación de pedidos.
- Es difícil gestionar picos de demanda.
¿Cómo optimizarlo?
- Usa Pick to Light para acelerar el picking y reducir errores.
- Incorpora wearables inteligentes (pulseras o guantes de picking) para optimizar el trabajo de los operarios.
- Implementa sistemas automáticos para tener siempre disponible la pieza que necesitas.
4. Falta de trazabilidad en tiempo real
Si no puedes saber en tiempo real dónde están tus productos dentro del almacén o la planta, estás perdiendo control sobre tu producción y logística.
¿Por qué es un problema?
- Se pierden productos dentro del almacén.
- Se generan retrasos en la producción o en la entrega.
- No hay un control eficiente ante auditorías o problemas de calidad.
¿Cómo optimizarlo?
- Implementa RFID o códigos de barras para rastreo en tiempo real.
- Utiliza software de trazabilidad para visualizar el flujo de materiales.
- Diseña circuitos logísticos con menos puntos de error.
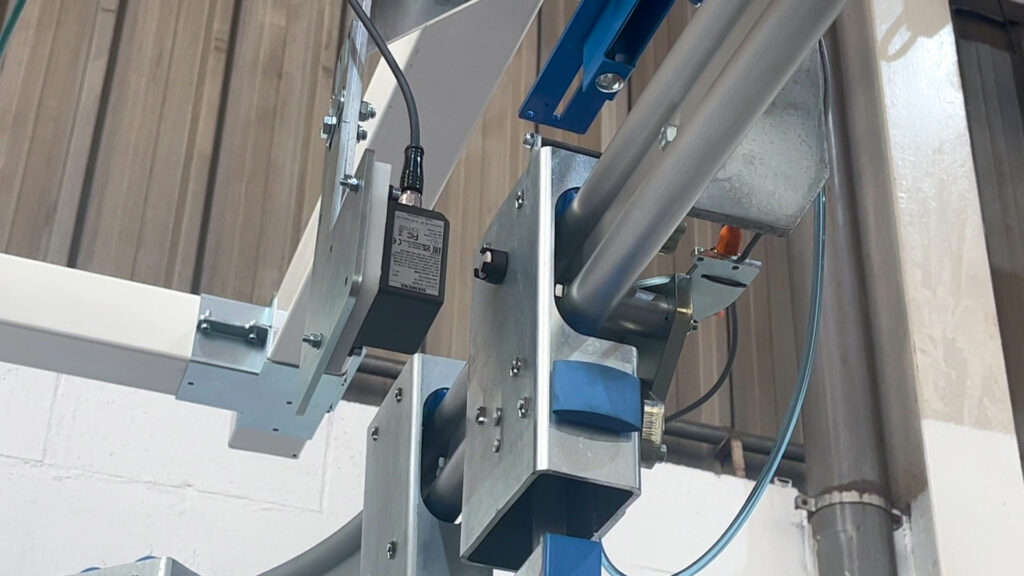
5. Almacenamiento sin estrategia
Almacenar sin lógica de rotación o sin optimizar el espacio disponible es una práctica que hay que evitar ya que impacta directamente en los costes logísticos.
¿Por qué es un problema?
- Los productos pueden caducar o volverse obsoletos.
- Se pierden productos dentro del almacén.
- El acceso a los materiales no es eficiente.
¿Cómo optimizarlo?
- Implementa un sistema FIFO (First In, First Out) para productos perecederos.
- Aplica LIFO (Last In, First Out) en productos de alta rotación.
- Usa almacenes dinámicos y sistemas de almacenamiento en altura para optimizar el espacio.
6. Falta de integración con otras áreas de la empresa
Muchas empresas aún operan con sistemas de gestión independientes que no se comunican entre sí, lo que genera ineficiencias y errores en la cadena logística.
¿Por qué es un problema?
- La información está fragmentada y no fluye correctamente.
- Se realizan procesos manuales innecesarios, aumentando el riesgo de errores.
- Es difícil reaccionar rápidamente a cambios en la demanda o incidencias operativas.
¿Cómo optimizarlo?
- Implementa un Sistema de Gestión Integrado (ERP) para centralizar la información.
- Automatiza procesos clave para reducir errores y tiempos muertos.
- Adopta tecnologías como Internet de las Cosas (IoT) o Inteligencia Artificial (IA) para una optimización intralogística.
7. Falta de planificación y simulación de flujos logísticos
Muchas empresas, tanto pequeñas como grandes, operan sin un diseño optimizado de sus flujos de materiales, lo que genera ineficiencias, tiempos muertos y desaprovechamiento de recursos.
Para las PYMEs, esto puede traducirse en un espacio mal aprovechado y operaciones desordenadas. Para grandes fabricantes, significa cuellos de botella en la producción y costes ocultos que afectan la rentabilidad.
¿Por qué es un problema?
- Se generan recorridos innecesarios, aumentando el tiempo de manipulación de productos.
- Se desaprovecha el espacio, lo que obliga a realizar más movimientos de los necesarios.
- Sin una planificación clara, es difícil prever problemas operativos y optimizar procesos.
¿Cómo optimizarlo?
- Analiza el layout del almacén y reorganiza recorridos de picking y transporte de materiales.
- Usa software de simulación logística para modelar y optimiza los flujos de trabajo antes de hacer cambios.
- Aplica principios Lean para reducir tiempos muertos y mejora la eficiencia sin necesidad de grandes inversiones.
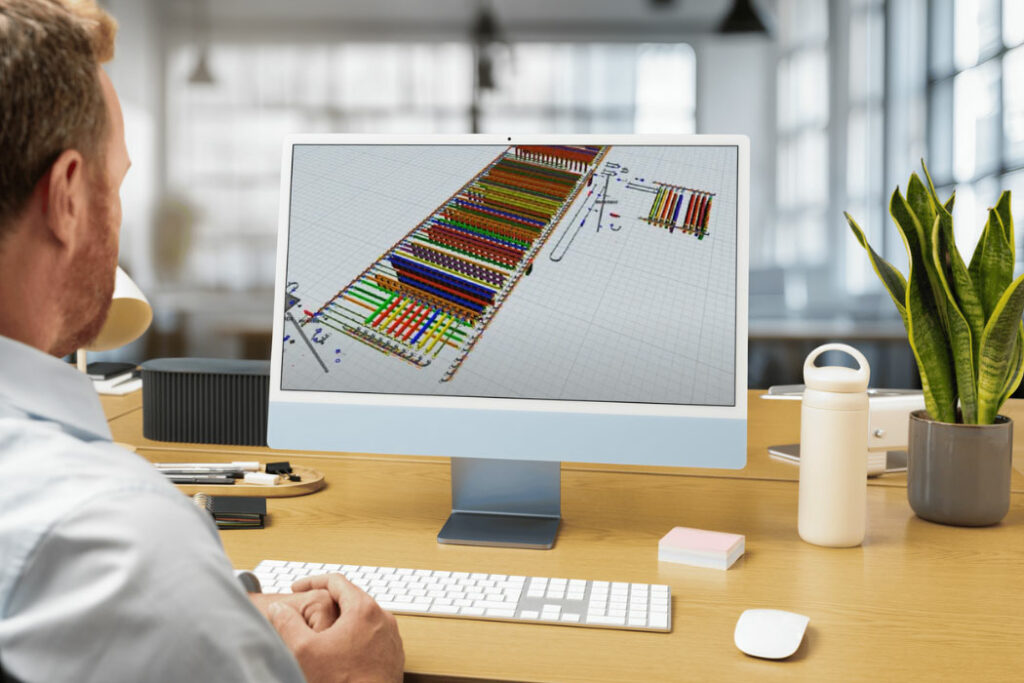
¿Cómo lograr una verdadera optimización intralogística?
No todas las empresas enfrentan los mismos retos logísticos ni requieren las mismas soluciones. El sistema ideal depende de múltiples factores, como el tipo de producto, el volumen de operaciones, la disponibilidad de espacio y el presupuesto.
Por eso, antes de hacer cambios drásticos, es clave detectar estas prácticas obsoletas y aplicar soluciones personalizadas que impulsen una optimización intralogística real. Contar con expertos en el diseño y mejora de flujos logísticos puede marcar la diferencia entre una simple mejora y una transformación eficiente y sostenible.
En Esypro, estudiamos cada caso de forma personalizada para diseñar la solución más eficiente según las necesidades específicas de cada cliente. Nuestro objetivo es actualizar tu logística interna sin necesidad de cambios radicales en tu nave.
Contáctanos y descubre cómo podemos ayudarte a transformar tu operación.