En 2023, Esypro colaboró con una destacada empresa Tier 1 en EEUU, especializada en la fabricación de parachoques para la industria automotriz, en busca de un nuevo sistema de conveyor. Teníamos un objetivo claro: transformar su gestión de almacenamiento e inspección de calidad. Gracias a nuestras soluciones, como los sistemas Esyconveyor Power & Free y Almaflex, logramos mejorar dos áreas clave: el almacenamiento de low runners y el control de calidad de las piezas.
En este artículo, te mostramos cómo nuestros sistemas ayudaron a un cliente a optimizar su operación. Esto permitió liberar espacio y garantizar un flujo de trabajo más eficiente.
Transportadores aéreos de preinspección: Flujos de trabajo sin contratiempos
En la fabricación de cualquier pieza de un automóvil, la calidad es fundamental para garantizar que cumpla con los altos estándares de la industria automotriz. La implementación de un sistema de preinspección asegura que solo las piezas adecuadas lleguen a la línea de montaje, evitando contratiempos y reduciendo el desperdicio.
Para lograr este objetivo, Esypro instaló dos circuitos Esyconveyor Power & Free: uno destinado a las defensas delanteras y otro a las traseras. Ambos sistemas están diseñados para manejar hasta 51 ganchos por conveyor, operando con un tiempo de ciclo de 60 segundos. Esto permite una inspección continua y eficiente de las 14 referencias de defensas, minimizando el tiempo perdido en caso de retrabajo.
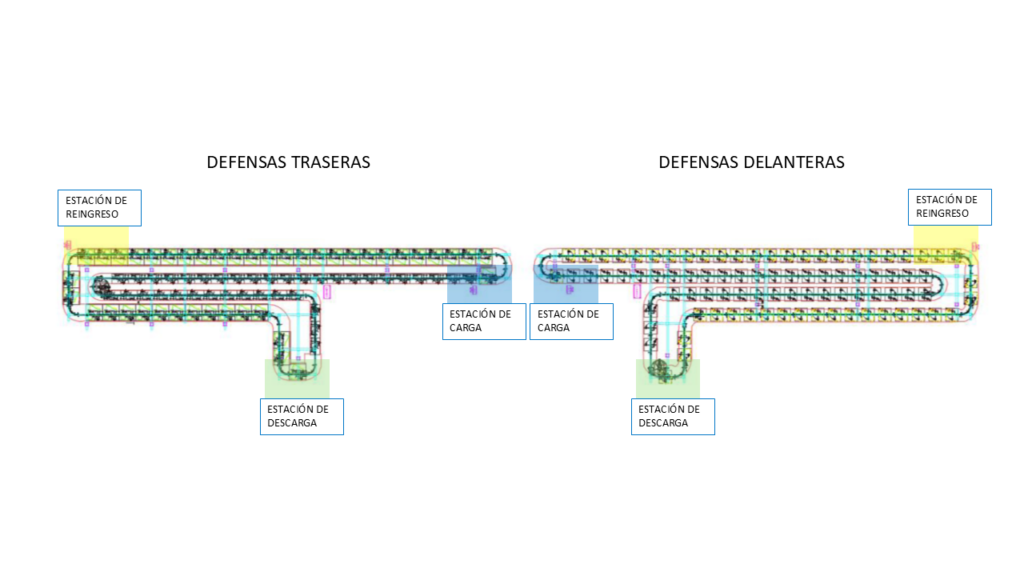
Inspección cercana al punto de carga
El proceso comienza antes de que la pieza se integre al conveyor. Muy cerca de la estación de carga, una persona operaria especializada inspecciona visualmente cada defensa para detectar cualquier defecto antes de cargarla en el gancho. Esta verificación inicial es crucial. Permite identificar y separar cualquier pieza que no cumpla los requisitos de calidad, asegurando que solo las defensas en condiciones óptimas ingresen a la secuencia.
Una vez que la pieza ha sido inspeccionada y aprobada, el operario/a cuelga la defensa en un gancho vacío, detenido en una estación de parada. Para iniciar el proceso, la persona operaria valida el sistema tirando de una cuerda, lo que desencadena una serie de comprobaciones automáticas. El sistema verifica la presencia de la defensa y lee la etiqueta para asegurar que la pieza esté en la secuencia correcta. Si la información es adecuada y hay espacio en la siguiente estación, el gancho se libera y avanza. Si la etiqueta no coincide o hay un error, el gancho se detiene. En ese caso, la persona operaria debe intervenir desde la interfaz HMI (Human Machine Interface).
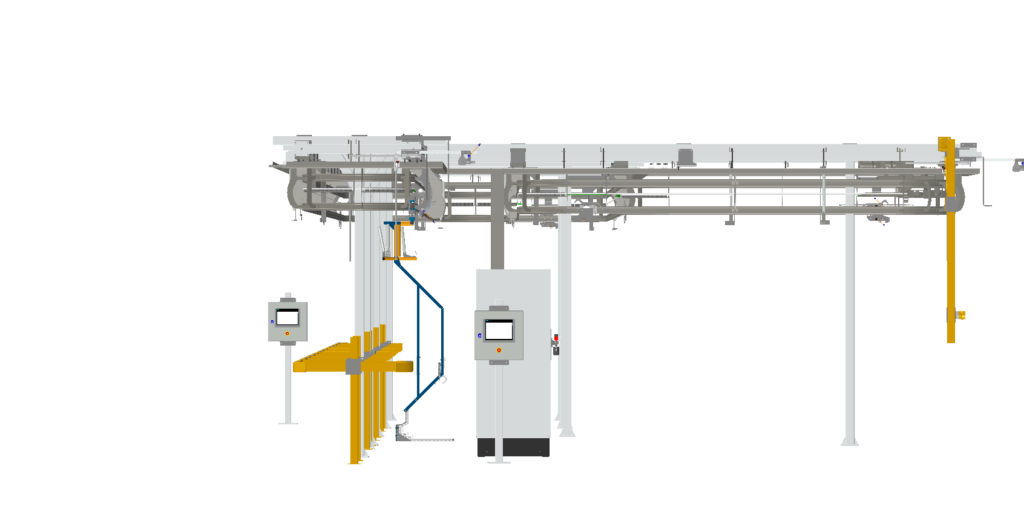
Estación de reingreso: Completando la secuencia
Estos transportadores también incluyen una estación de reingreso, diseñada para asegurar que las piezas que requirieron retrabajos se reincorporen al flujo de manera controlada. En esta estación, después de cargar la defensa corregida, el sistema lee nuevamente la etiqueta del gancho para confirmar que la pieza sigue la secuencia adecuada. Si la etiqueta es correcta, el gancho se libera automáticamente y avanza hacia la siguiente etapa. Si la pieza es incorrecta o falta, el gancho se detiene en la estación de parada automática. Ahí queda a la espera de la validación manual de la persona operaria a través de la HMI.
Estación de descarga: Orden controlado
La última fase de esta zona de almacenamiento de preinspección es la estación de descarga. Aquí, la defensa que previamente ha pasado la inspección visual se detiene automáticamente para ser retirada por el operario/a. Después de recoger la pieza, la persona operaria valida el sistema tirando nuevamente de la cuerda. Así asegura que haya un gancho vacío disponible para reiniciar el circuito.
Tecnología RFID para una operación sin errores
La integración de la tecnología RFID en el sistema de preinspección es fundamental para garantizar un flujo continuo y sin errores. El sistema RFID detecta automáticamente cuándo una secuencia de piezas está completa, permitiendo que las piezas avancen en la cadena sin necesidad de intervención manual. Esta automatización facilita que la persona operaria se concentre en tareas que realmente aportan valor, como la inspección de calidad. Esto hace que el proceso sea más rápido y confiable.
Almacén de low runners: Liberando espacio con soluciones funcionales
En la producción automotriz, las piezas low runners presentan un desafío particular. Son aquellas piezas que se utilizan con menor frecuencia en el proceso de montaje, por lo que no se requieren de manera continua. Sin embargo, resultan fundamentales para ciertos pedidos específicos o en momentos puntuales de producción. Aunque su demanda es baja, su almacenamiento ocupa un espacio considerable en el almacén. Esto puede generar congestión y limitar la capacidad para gestionar otros elementos de mayor rotación.
Para solucionar este problema, Esypro diseñó un sistema que reorganiza el almacén de manera estratégica. Utiliza una plataforma elevada y el sistema Almaflex para aprovechar al máximo el espacio vertical sin comprometer la accesibilidad.
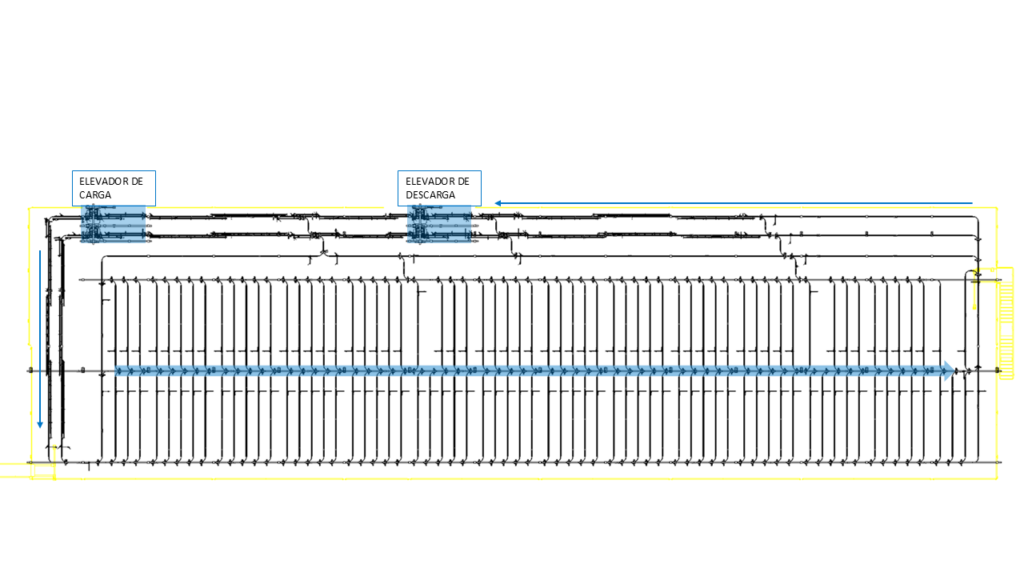
Aprovechamiento del espacio vertical
La propuesta de Esypro fue instalar una plataforma peatonal elevada que liberara el suelo de la planta. Esto creó un área específica para almacenar las defensas low runners. Este enfoque redujo la congestión en las áreas de trabajo y permitió que el espacio en planta se destinara a operaciones de mayor rotación. Así, se mejoró la eficiencia general del almacén.
Sobre la plataforma se instaló el sistema Almaflex, que facilita el almacenamiento y la recuperación de defensas de forma manual. Aprovecha la altura disponible sin necesidad de realizar cambios estructurales complejos. El transporte de piezas entre niveles se realiza mediante dos elevadores: uno de carga y otro de descarga. Ambos cuentan con pequeñas zonas de almacenamiento automatizadas en el nivel superior. Los empujadores automáticos desplazan los ganchos hacia y desde el elevador, eliminando la necesidad de intervención manual en esta parte del proceso.
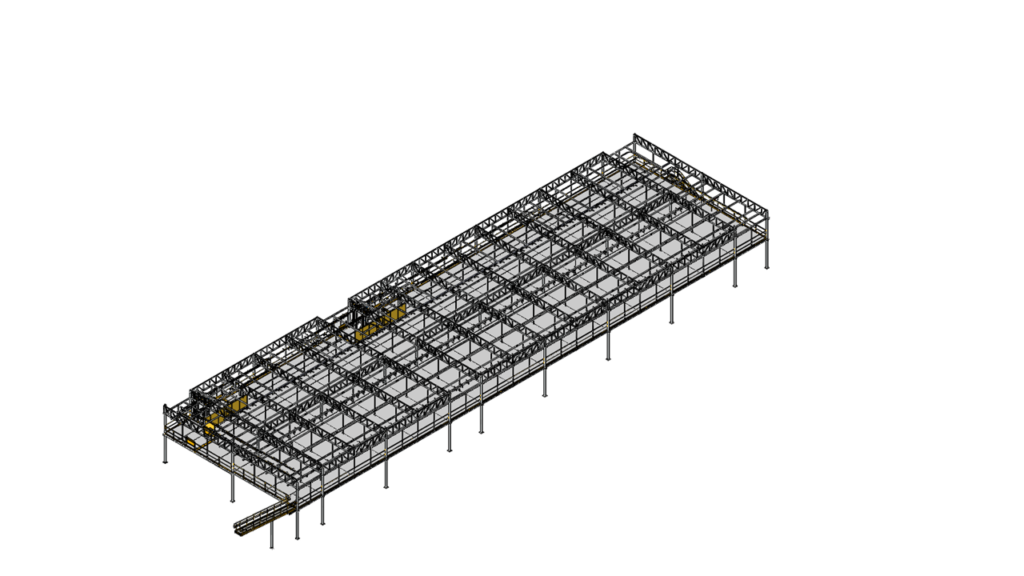
Carga eficiente y buffer de ganchos vacíos
El proceso de carga comienza en la planta inferior. Una persona operaria coloca una defensa low runner en el elevador de carga, después de que un gancho vacío descendiera automáticamente desde el nivel superior.
Una vez que el gancho está cargado con una defensa, el elevador lo transporta al segundo nivel. Allí se establece otro buffer que facilita la transición hacia el sistema de almacenamiento. Este proceso automatizado mantiene un flujo de trabajo continuo, evitando que el personal pierda tiempo en tareas repetitivas o en la espera de disponibilidad del sistema.
Es importante mencionar que en la parte superior hay un pequeño buffer de ganchos vacíos antes del elevador de carga. Este buffer asegura que siempre haya suficientes ganchos disponibles para realizar una carga. Los ganchos son empujados automáticamente al elevador mediante empujadores.
Almacenamiento en las barras de acumulación
Desde el buffer situado después del elevador, una persona operaria mueve los ganchos con piezas hacia las barras de acumulación del sistema Almaflex. Estas barras están diseñadas para organizar las defensas de manera accesible y ordenada. Cuentan con desvíos dobles en sus extremos, lo que facilita la introducción de piezas. La persona operaria puede dirigir el gancho hacia la barra adecuada, asegurando que cada tipo de defensa esté correctamente ubicada.
Cuando se necesita una defensa específica, la persona operaria extrae los ganchos del extremo opuesto de las barras de acumulación y los incorpora a una secuencia que se dirige al elevador de descarga. Esta operación se realiza en un pasillo central entre los dos frentes de almacén. En ese pasillo, la persona operaria utiliza desvíos triples para seleccionar la referencia correcta y añadirla a la secuencia.
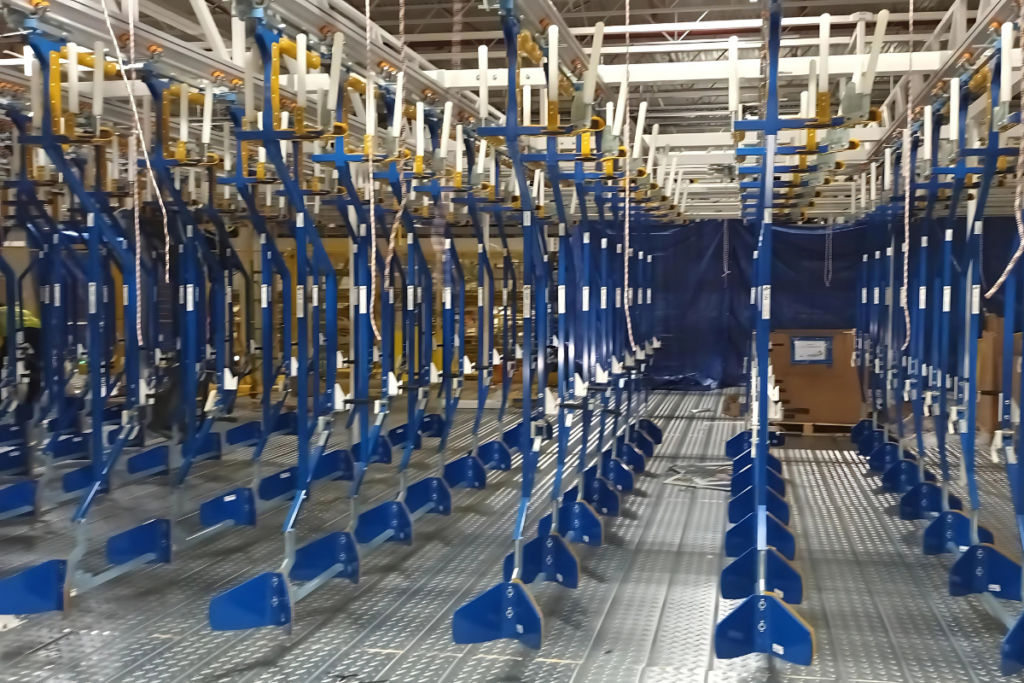
Descarga ordenada y con atajos
Una vez que la secuencia está completa, los ganchos cargados se agrupan en un pequeño buffer antes del elevador de descarga. Los empujadores automáticos transportan los ganchos al elevador, que baja las piezas al nivel inferior para que otra persona operaria las recoja. Mientras tanto, los ganchos vacíos regresan automáticamente al sistema, listos para ser reutilizados.
Para situaciones donde se necesita una pieza con urgencia y no hay tiempo para esperar a que la secuencia habitual llegue al punto de descarga, se implementó una Fast Line. Esto permite que la persona operaria envíe manualmente una pieza específica por un camino rápido. De esta manera, se supera el flujo regular y se asegura su disponibilidad inmediata.
Integración y sincronización del proceso
El sistema Almaflex y los elevadores se integran de manera eficiente con el trabajo del equipo humano, creando un flujo de trabajo perfectamente sincronizado. Esto reduce los movimientos innecesarios y asegura que las piezas estén disponibles justo cuando se necesitan. Se evitan así cuellos de botella y se maximiza la agilidad de la operación. Además, la flexibilidad del sistema permite adaptarse a cambios en las necesidades de almacenamiento. Esto resulta ideal para plantas que requieren ajustes continuos en su gestión de inventarios.
Resultados: Soluciones eficientes que generan satisfacción
El impacto de estas soluciones fue inmediato. El cliente alcanzó una organización más eficiente en su almacén, eliminando las congestiones que podían afectar el flujo de trabajo. La implementación del sistema de almacenamiento vertical no solo liberó espacio crítico en la planta, sino que también mejoró la accesibilidad a las piezas low runners. Esto permitió una respuesta más rápida a las demandas de producción.
La instalación de los buffers de preinspección facilitó un control de calidad sin interrupciones, evitando que piezas defectuosas avanzaran a las etapas finales de producción. No solo se redujeron los errores, sino que también se optimizó el trabajo del personal, integrando un flujo de materiales ordenado y secuenciado.
Lo más destacado de este caso es que todo se logró sin añadir complejidad innecesaria. Las soluciones de Esypro están diseñadas para integrarse de manera fluida en las operaciones existentes, mejorando el rendimiento sin interrumpir la producción. El cliente quedó plenamente satisfecho con el impacto de estos cambios, observando una transformación significativa en la eficiencia de su planta.
Simplicidad y eficacia en cada proyecto
Este caso demuestra cómo Esypro aborda los desafíos industriales con un enfoque centrado en la simplicidad y la eficacia. A través de la implementación de sistemas como Esyconveyor y Almaflex, no solo optimizamos el uso del espacio, sino que también mejoramos los procesos operativos y los flujos de trabajo. Nuestra filosofía es clara: soluciones prácticas que resuelven problemas reales y generan resultados tangibles.
En cada proyecto, adaptamos nuestras soluciones a las necesidades específicas de cada cliente. Si buscas transformar la operativa de tu planta, no dudes en contactarnos.